Гриндер из двигателя от блендера
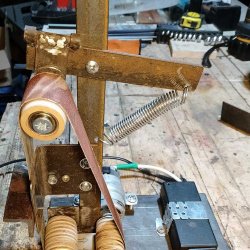
Когда-то давно, заинтересовал меня такой инструмент как гриндер (шлифовальный ленточный станок). Устройство его мне показалось не очень сложным и я задумал его изготовить. В обзоре довольно много слов и фото. Описаны как правильные шаги, так и ошибочные.
Еще в те времена заказал на Али комплект из 10 подшипников 608ZZ: d=8 x D=22 x B=7 mm.
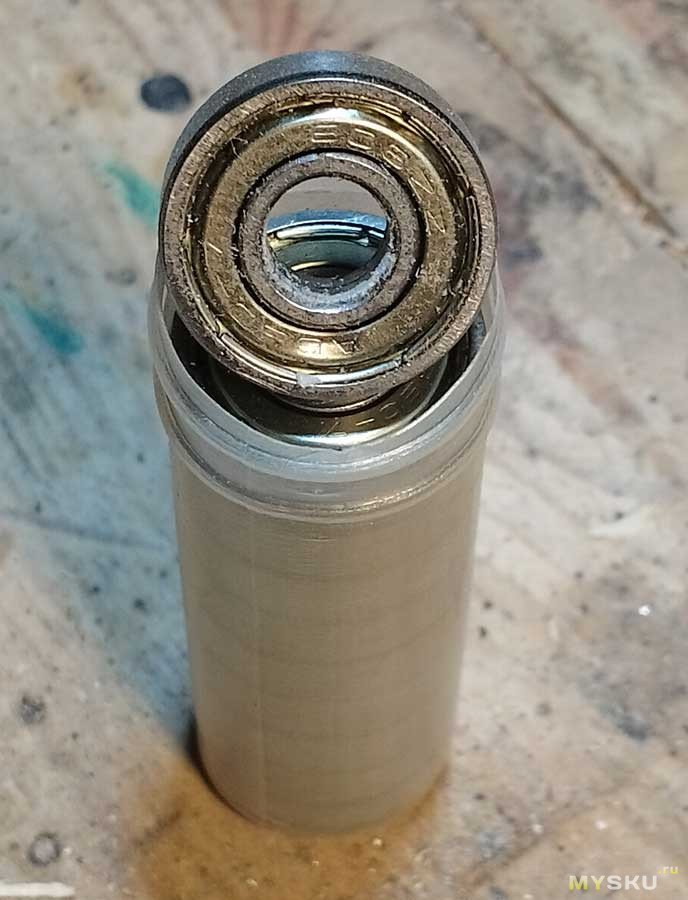
Однако, возможности изготовить тогда у меня не было: ни необходимого инструмента, ни места для изготовления.
Не очень давно, в закромах обнаружился старый электродвигатель от советской стиральной машины, который когда-то выполнял роль точила.
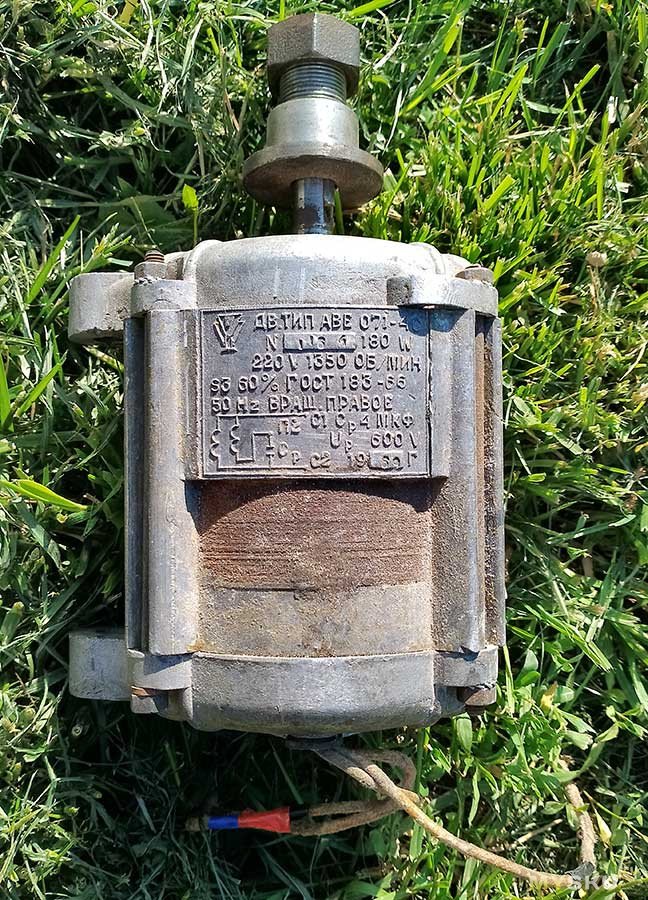
И идея сделать гриндер возникла вновь.
После того, как двигатель был приведен в рабочее состояние, начал просматривать информацию. Вернее выбирать конструкцию из различных самоделок, видео ролики которых есть в интернете.
Параллельно знакомился с теоретической частью.
Для разных материалов требуется разная скорость движения ленты. На рисунке ниже рекомендуемые скорости для разных материалов.
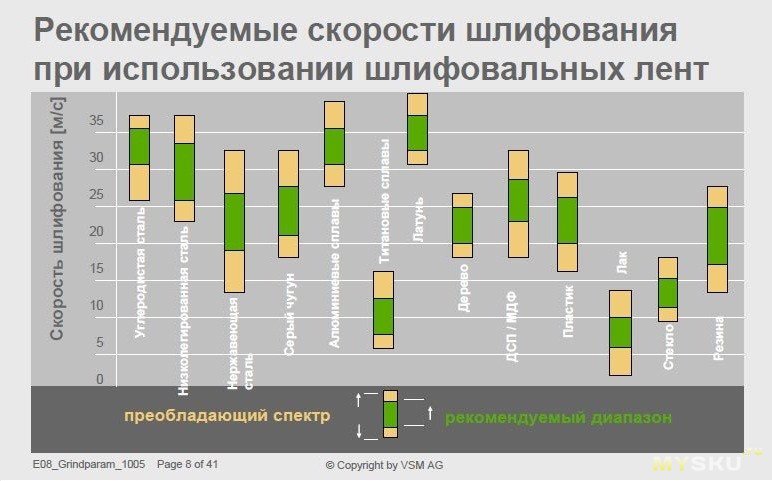
Получалось, что средняя скорость, которая бы подошла для многих примерно 20 м/с.
Исходя из этого параметра нужно было изготовить ведущий ролик, который крепится на вал двигателя.
Не буду утомлять выкладками. Скорость движения ленты рассчитывается по формуле
V = pi * D * n/(60 * 1000), где
V — скорость движения ленты в м/с
D — диаметр ролика в мм
n — количество оборотов двигателя в минуту
pi — известная константа.
Откуда диаметр ролика D = V * 60 * 1000 /(pi * n).
Таким образом, чтобы достичь необходимой скорости ленты для этого двигателя понадобится ролик диаметром 20*60000/(3,14*1350) = 283 мм.
Мне показалось, что он несколько великоват.
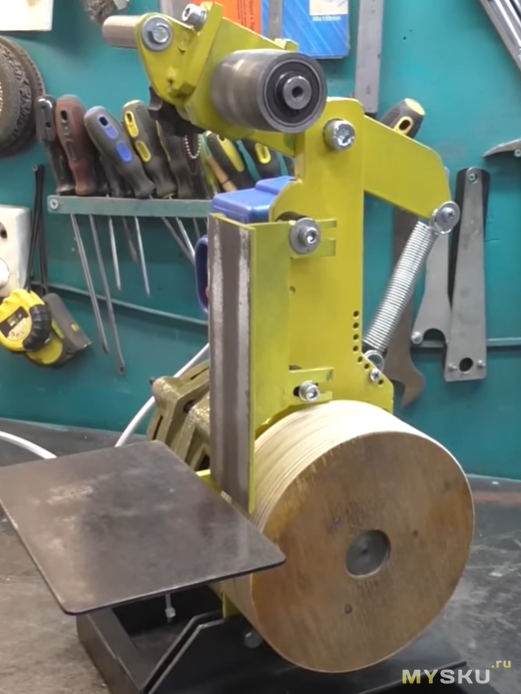
Однако идея изготовить станок уже поселилась в моей голове, и я стал искать другие варианты.
Среди объявлений на OLX обнаружил продажу б/у двигателей от разных современных стиральных машин. Стоимость такого двигателя примерно $10.
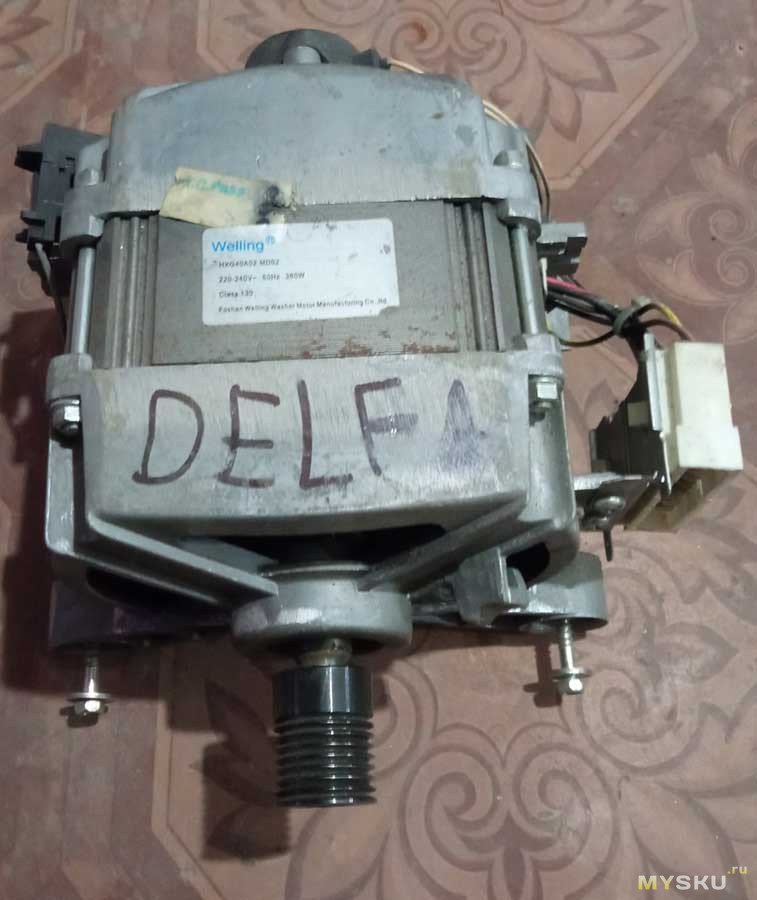
Максимальная скорость вращения 13000-16000 оборотов в минуту.
Таким образом, диаметр ролика мог быть порядка 30 мм.
Еще одним плюсом было то, что на Али есть масса предложений регуляторов оборотов для таких двигателей.
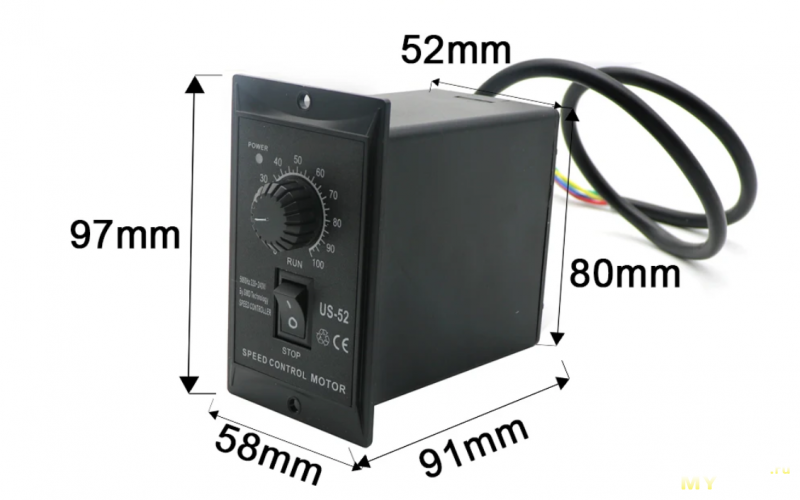
На OLX было много предложений бесколлекторных или индукционных двигателей. Однако, я так и не нашел устройства, с помощью которого такой двигатель можно было включить.
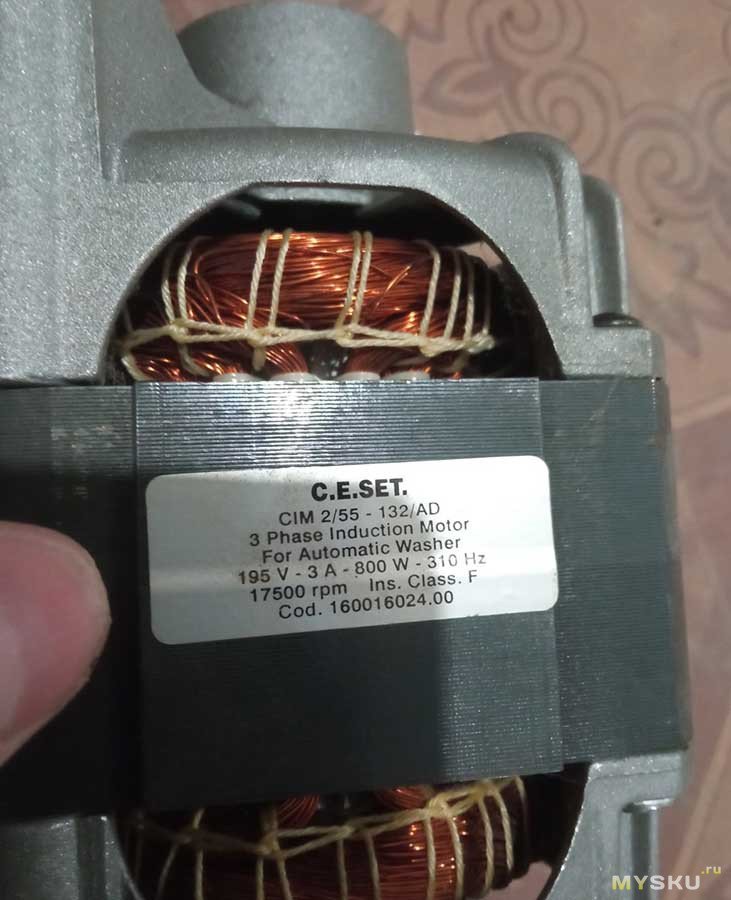
Но тут я подумал, а зачем мне такой громоздкий агрегат на рабочем столе? Пользоваться я буду им не очень часто, даже пока не знаю где можно его применить. Может заточка сверл, ножей или еще чего.
Более миниатюрный вариант можно изготовить из двигателя от шуруповерта, например.
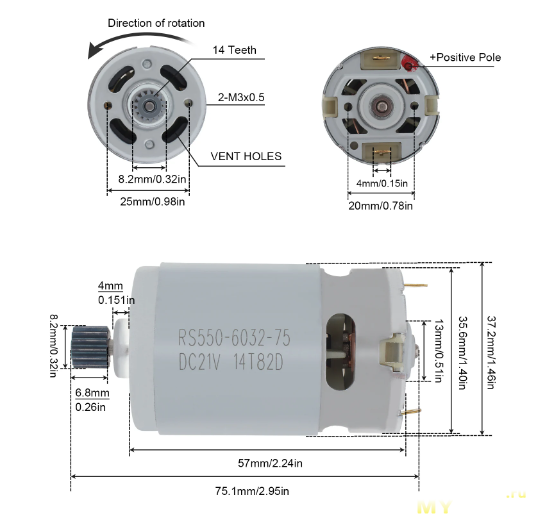
Однако, мощность такого двигателя довольно маленькая порядка 90-100Вт.
И тут на глаза попался моторный блок от старого блендера. Правда, мощность именно этого варианта была тоже не очень большой — 300Вт.
На том же OLX можно найти много предложений моторных блоков или даже блендеров с поломанными чашами или другими частями ценой от $5.
Но мне повезло еще больше. В разговоре один из знакомых сказал, что у него валяется такой моторный блок, и он с удовольствием его мне отдаст.
Это оказался блок от блендера Philips HR1372.
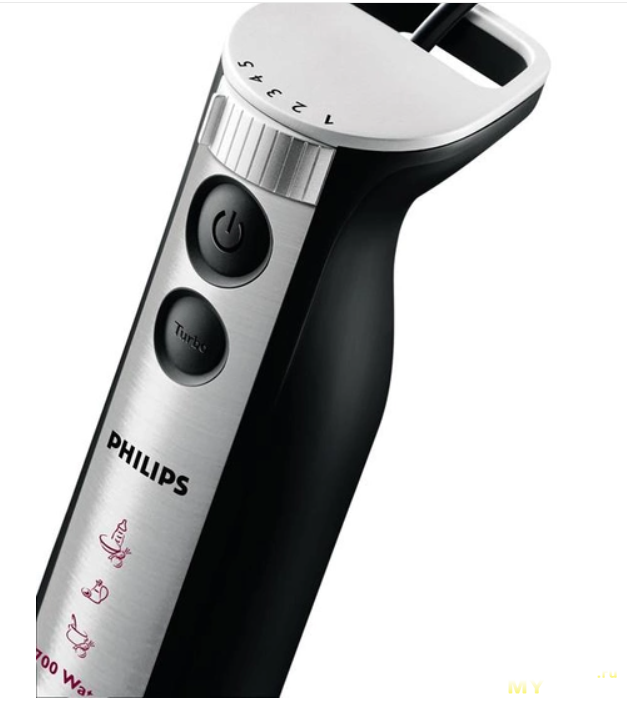
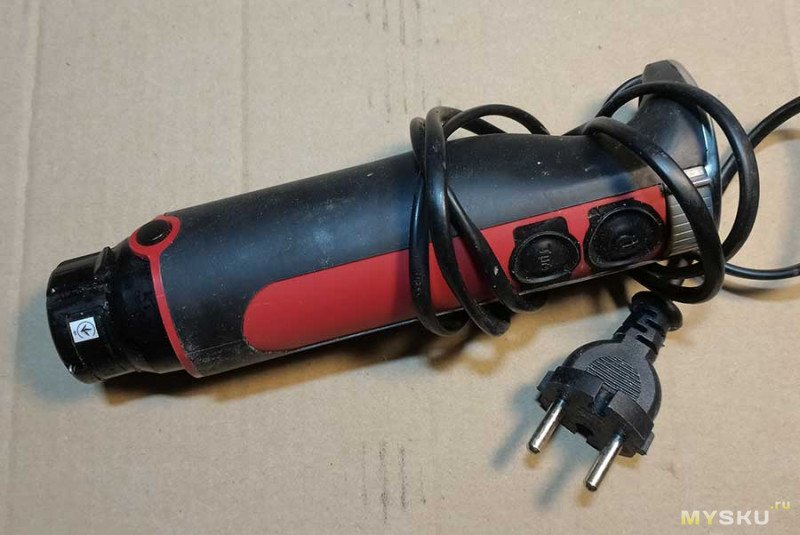
Внутри двигатель WRS-7912PM. Мощность 700Вт. Небольшие размеры еще и регулятор оборотов в наличии. Идеальный вариант.
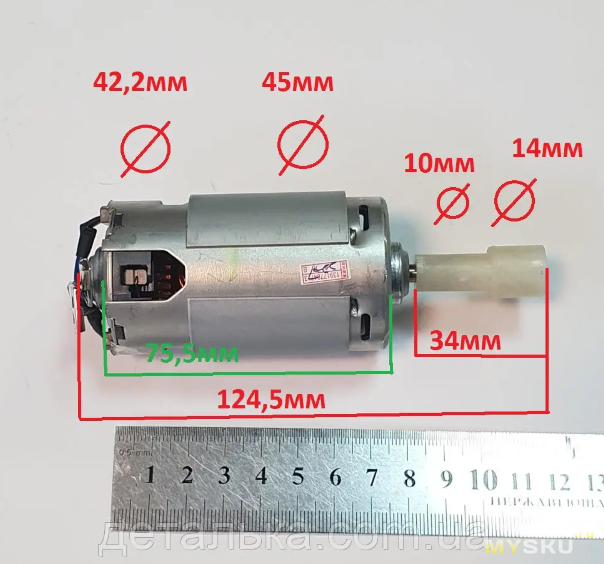
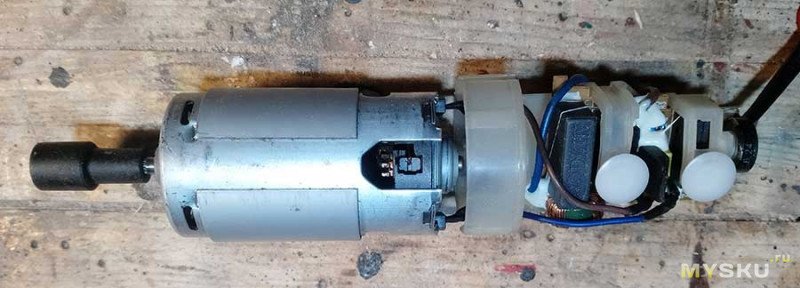
Однако, мне никак не удавалось найти информацию о скорости вращения.
ИИ любезно сообщил, что скорость оборотов бытовых блендеров примерно 10000 оборотов в минуту. Что в общем тоже отлично подойдет для гриндера.
Но мне хотелось точнее узнать скорость конкретного двигателя. И опять поиски в интернете. Вариантов как определить скорость довольно много. Но в основном они подходят для трехфазных двигателей с небольшим количеством оборотов, порядка 1000.
Наконец мне удалось найти отличный способ. Идея состоит в том, что на вал двигателя крепится небольшой неодимовый магнит. Я отломал кусок от магнита из HDD. Далее необходим тестер, умеющий измерять частоту. Такой тоже у меня нашелся, который был приобретен не так давно.
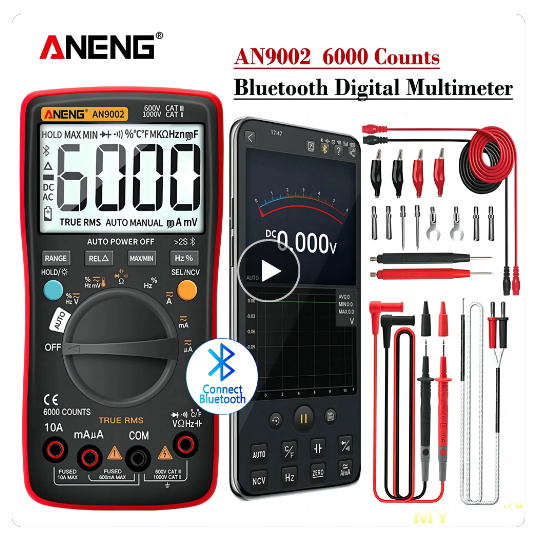
К щупам подключается любая катушка. На сколько я понимаю, чем больше витков будет, тем лучше. Я выпаял небольшой трансформатор с платы телевизора и вытащил из него сердечник.
Двигатель включается, катушка подносится к вращающемуся валу. На тестере возникает частота в герцах (количество колебаний в секунду). Умножив ее на 60 получаем количество оборотов в минуту.
Измерения показали, что максимальные обороты двигателя 12000 обр.мин, а минимальные — 8200.
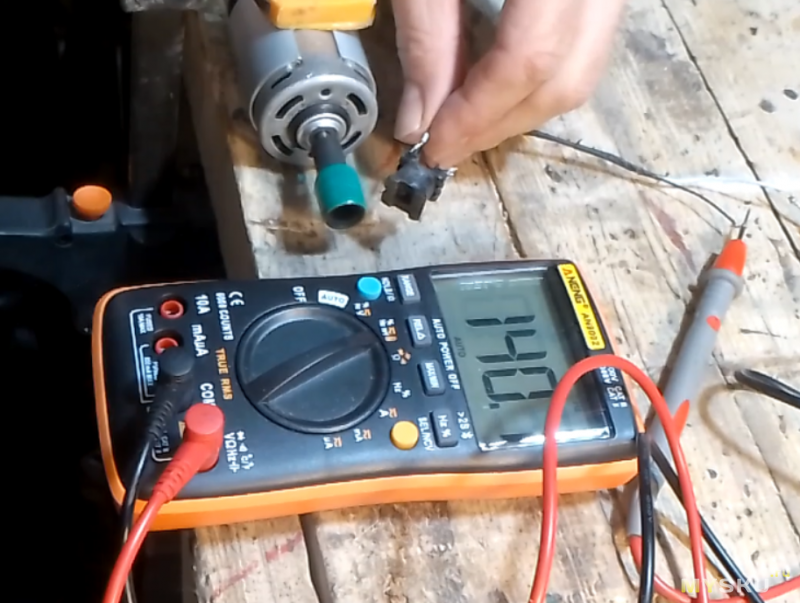
Для гриндера решил использовать ленту для шлифовальной машины длиной 533 мм и шириной 75 мм (по словам продавца самая популярная). 75 мм слишком широкая для такого двигателя, поэтому ленту разорвал пополам.
Следующим шагом было изготовить ведущий и пассивные ролики. Исходя из ширины ленты и оборотов двигателя ролик должен быть примерно 31 мм в диаметре и шириной 40 мм. На многих видео авторы рекомендуют использовать муфты бочкообразной формы. Это стабилизирует ленту.
Доступа к токарному станку у меня нет. Но в интернете полно идей как изготовить ролики без токарного станка.
Первая идея, это использовать соединительные муфты для пайки полипропиленовых труб. С муфтой для трубы 32 мм отлично подходят подшипники диаметром 32 мм. Внешний диаметр такой муфты 45 мм, а длина 40. Почти то что нужно. Кроме того, такие муфты уже есть бочкообразной формы.
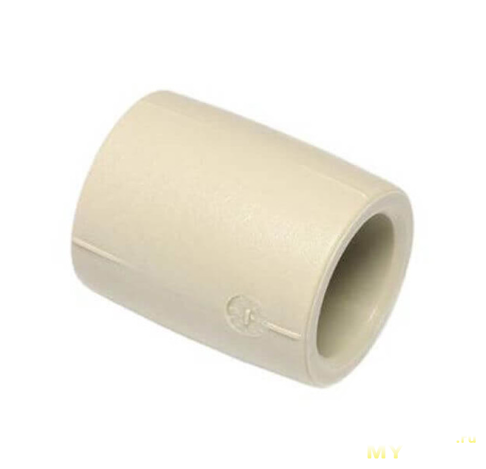
Но у меня в наличии подшипники диаметром 22 мм.
В закромах нашелся кусок трубы PN 20. Внешний диаметр 32 мм. То что доктор прописал.
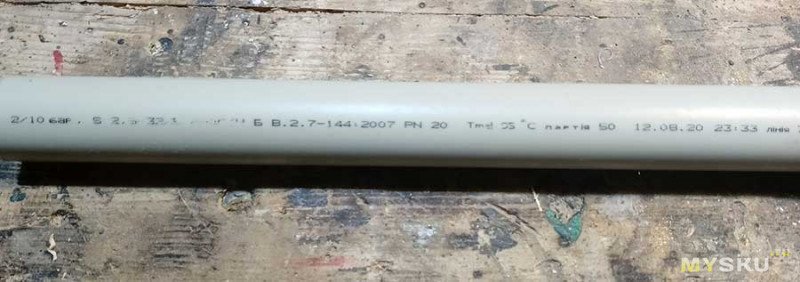
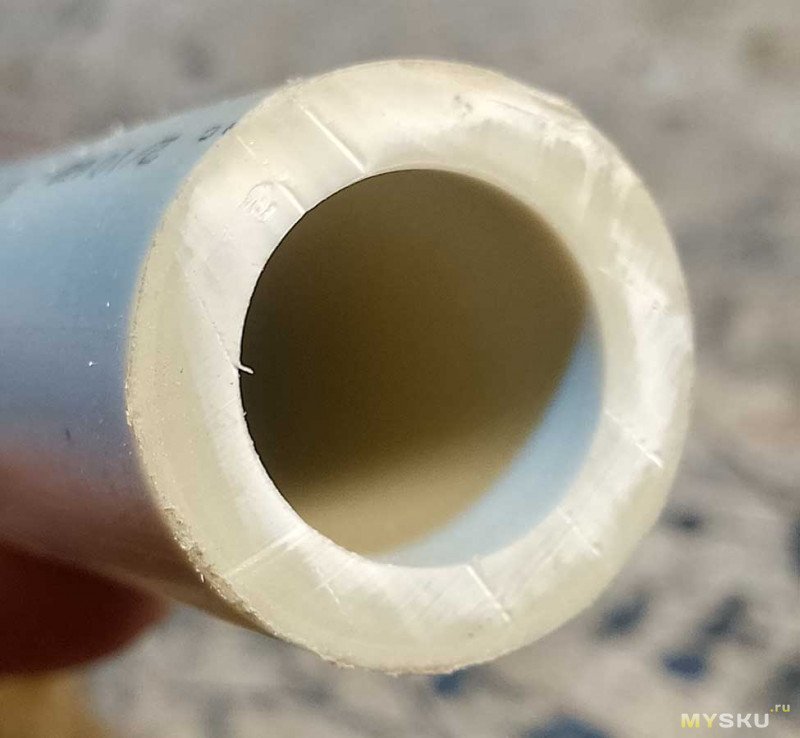
Были отрезаны два куска трубы, а также вставки из металлической трубки, чтобы подшипники не заклинило при затягивании на оси.
Подшипники легко запрессовались с помощью тисков. Но при этом труба расширилась в местах запрессовки.
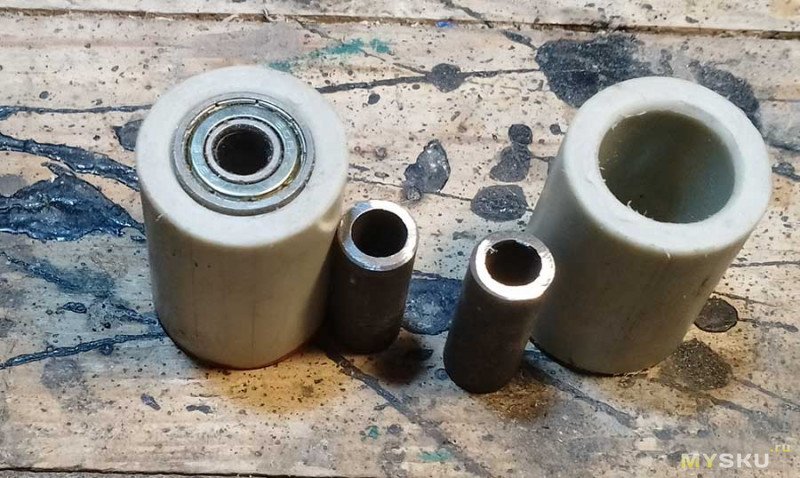
Но как я ни старался отрезать ровно полипропиленовую и металлическую трубы, мне это не удалось. В результате даже расхождения в пару миллиметров вызвало перекос подшипников относительно оси. Опять же, токарный станок в этом случае помог бы.
Следующей идеей было изготовить ролики из фанеры, вырезав из нее круги нужного диаметра и склеив друг с другом. В дрель была закреплена коронка для проделывания отверстий в гипсокартоне.
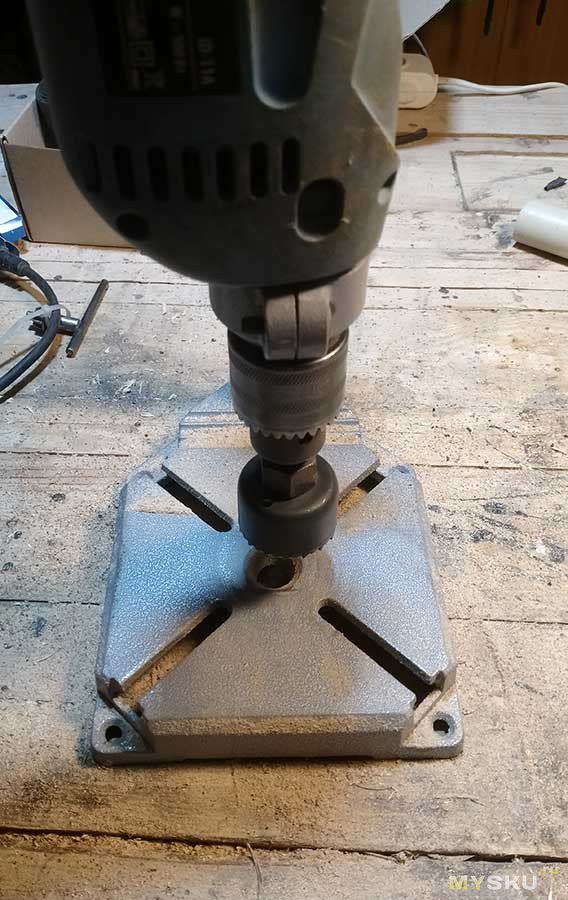
Как ни странно, она довольно легко справилась с поставленной задачей.
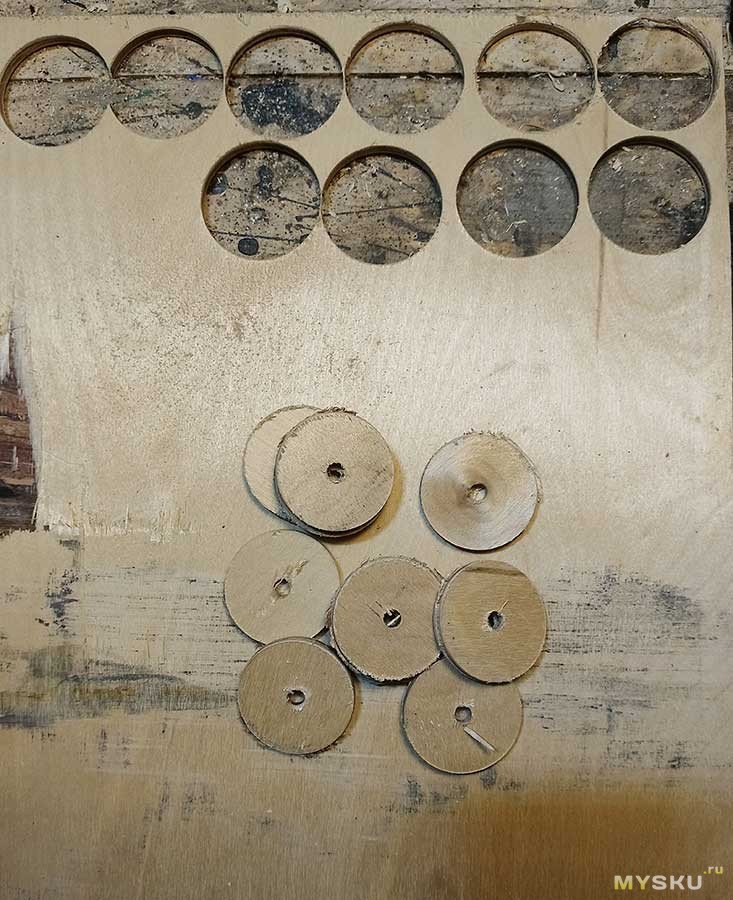
Затем круги последовательно одеваются на болт подходящего диаметра, каждый слой промазывается клеем (ПВА подходит) и этот слоенный пирог сжимается с помощью гаек и струбцин.
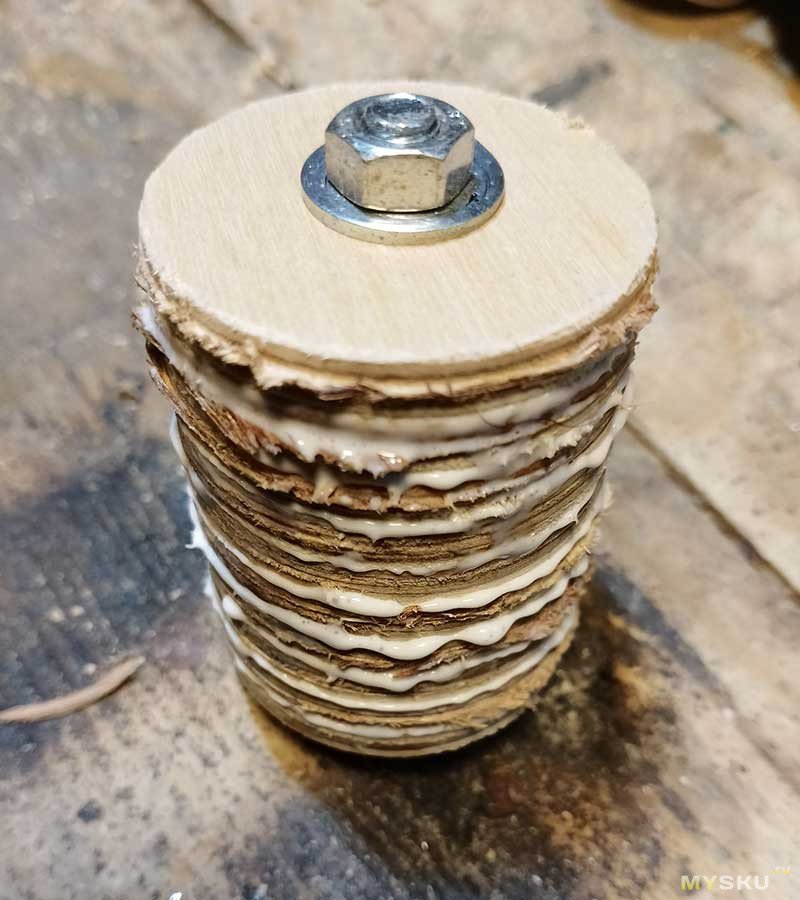
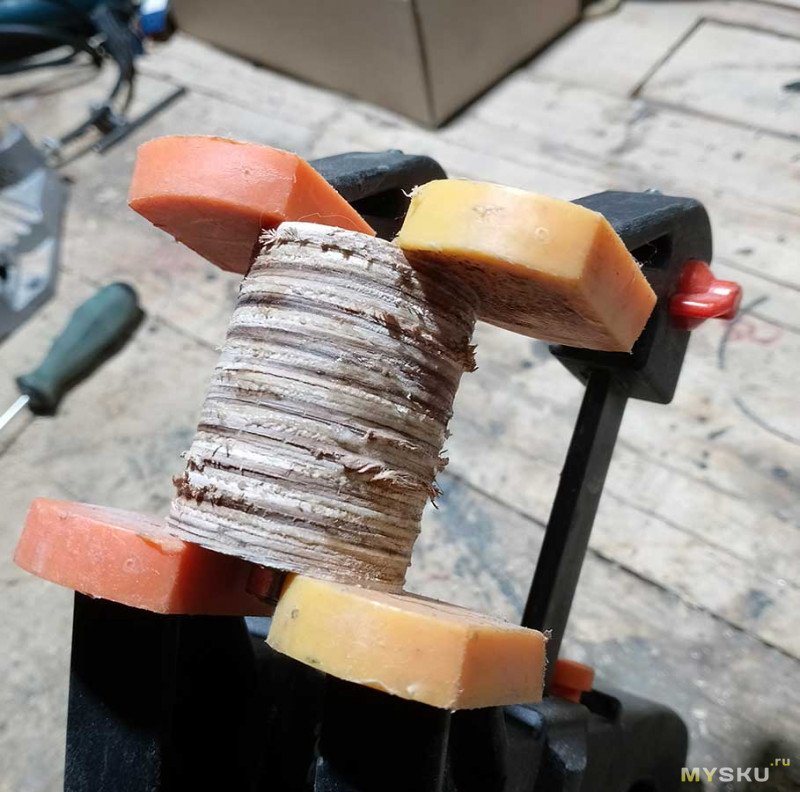
Лайвхак. Диаметр отверстия посередине круга примерно 6 мм. Желательно сразу рассверлить его до необходимого, в моем случае до 10мм, потому что внутренний диаметр подшипника 8 мм. Точно увеличить отверстие в уже готовом ролике намного сложнее и не всегда получается. Я испортил один таким образом.
После высыхания клея, оказалось, что болт плотно сидит внутри ролика и извлечь его можно только выкрутив. Эта особенность сослужила мне хорошую службу.
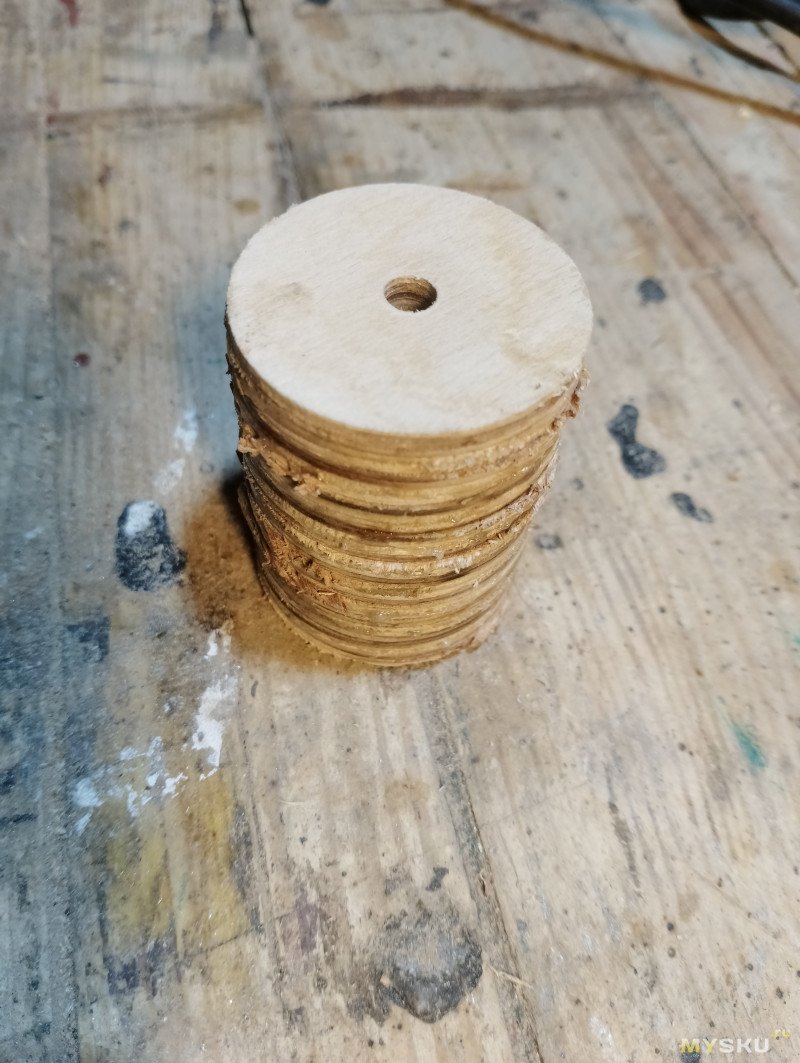
Диаметр склеенного ролика примерно 40 мм.
Но края ролика крайне неровные, а токарного станка нет.
Для дальнейшей обработки можно использовать обычную дрель. Стержень выкручивается из ролика таким образом, чтобы с одного края оставалось место на толщину подшипника плюс небольшой запас. За счет того, что стержень имеет резьбу, дополнительного крепления ролика не требуется.
Направление вращения дрели выбирается таким образом, чтобы ролик накручивался на стержень, т.е. против часовой стрелки.
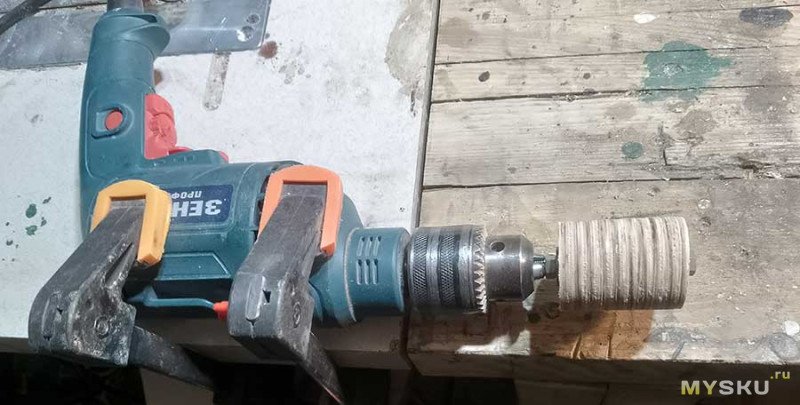
Далее идет обработка ролика как на токарном станке. Для обработки можно использовать например стамеску. Но мне больше понравилось обтачивать с помощью болгарки и шлифовального диска.
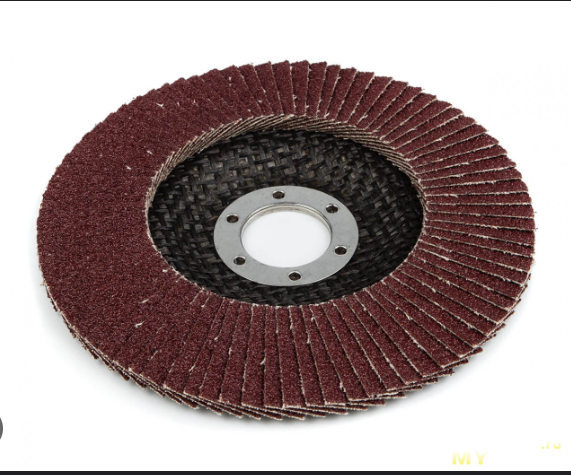
Опять же, направления вращения дрели и круга болгарки должны быть противоположными.
Таким образом ролик довольно быстро принимает нужную форму и гладкую поверхность.
В итоге получился ролик диаметром примерно 31 мм бочкообразной формы.
На двигателе есть пластиковая муфта диаметрами 10 и 14 мм.
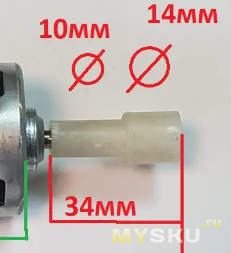
Более толстая часть была срезана. В одном из роликов было просверлено отверстие чуть меньше 10мм и ролик был посажен на клей.
Для остальных роликов нужно было изготовить посадочное место для подшипников.
Это делается с помощью все той же стамески на валу дрели.
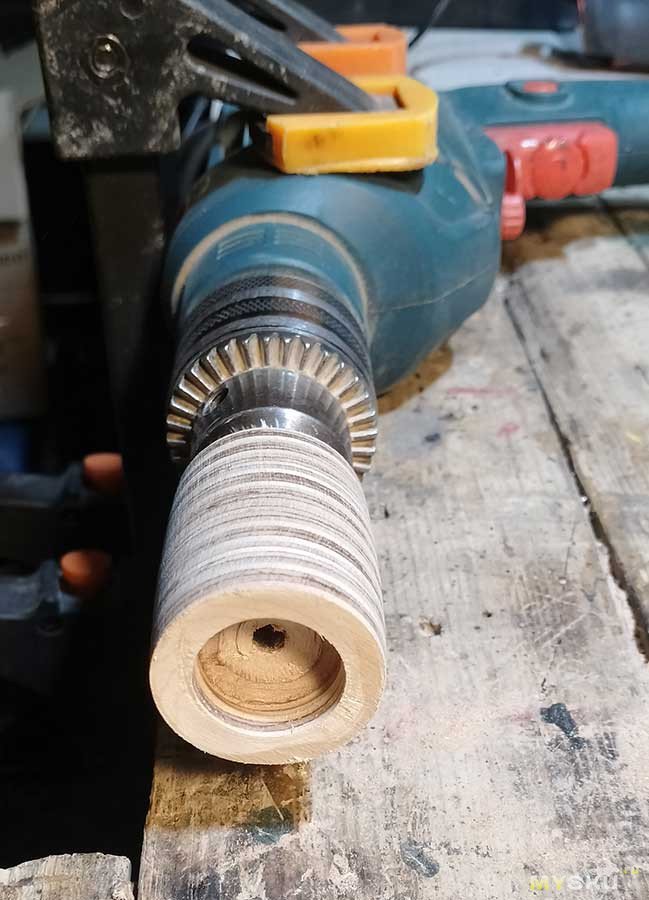
При постоянной примерке удалось достаточно точно изготовить посадочные места. Даже не вклеивал подшипники, а просто запрессовал.
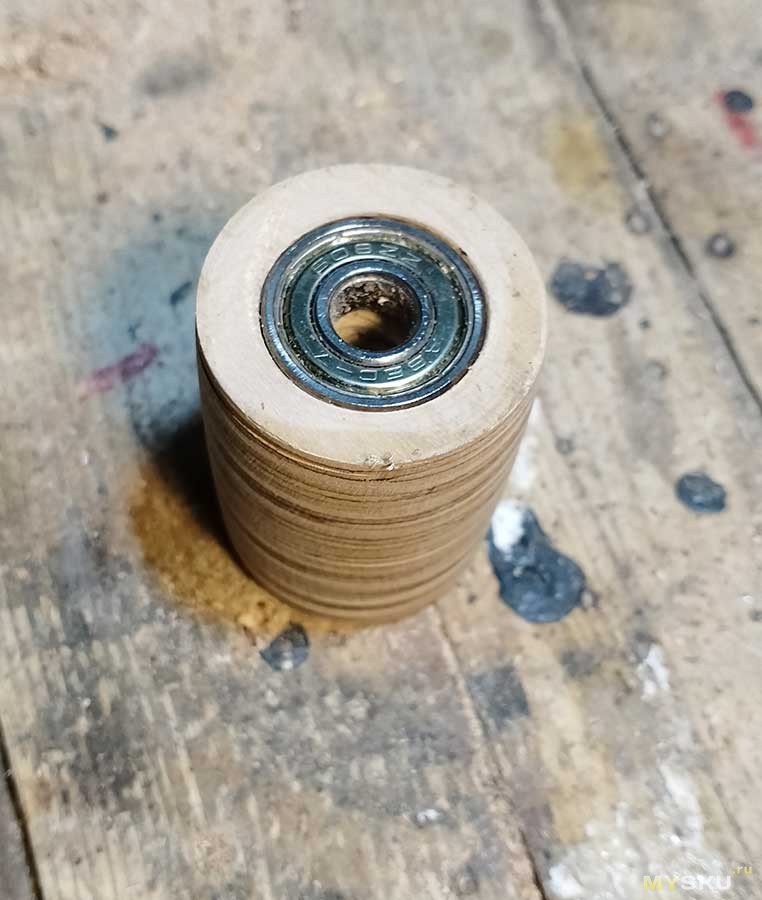
Далее нужно было изготовить собственно станину, на которой будут крепиться ролики и двигатель.
На пункте приема металлолома была приобретена металлическая пластина 220*120 мм и толщиной 3,5 мм.
К ней был приварен уголок 25 мм и внизу небольшой кусочек пластины для крепления нижнего ролика.
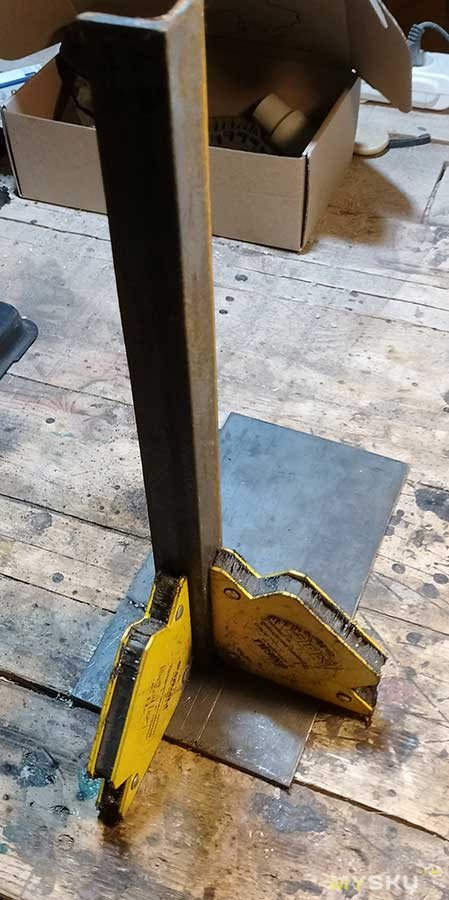
Двигатель был закреплен рядом с уголком с помощью хомута.
Далее нужно было сделать рычаг для верхнего ролика. Этот ролик должен быть подвижным, чтобы можно было натягивать ленту.
Рычаг изготовлен из куска стальной полосы шириной 25 мм и толщиной 3,5 мм Кроме того, ось верхнего ролика должена смещаться от горизонтального положения. Это необходимо чтобы регулировать ленту, когда она пытается уйти с роликов.
Сначала я приварил старую оконную петлю. Но это оказалось неудачным решением. Она довольно сильно выступала в сторону, кроме того, вал ролика нельзя было закрепить с помощью гайки. Пришлось делать навес самостоятельно.
Два небольших отрезка трубы в качестве петель. К куску все той же полосы приварен отрезок катанки подходящего диаметра. После того, как все это выставляется, отрезки трубки привариваются к полосе.
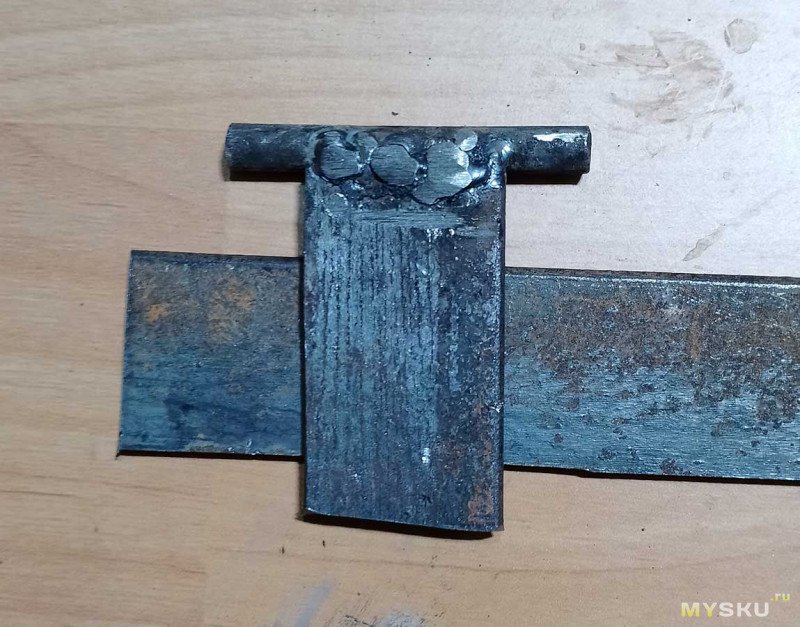
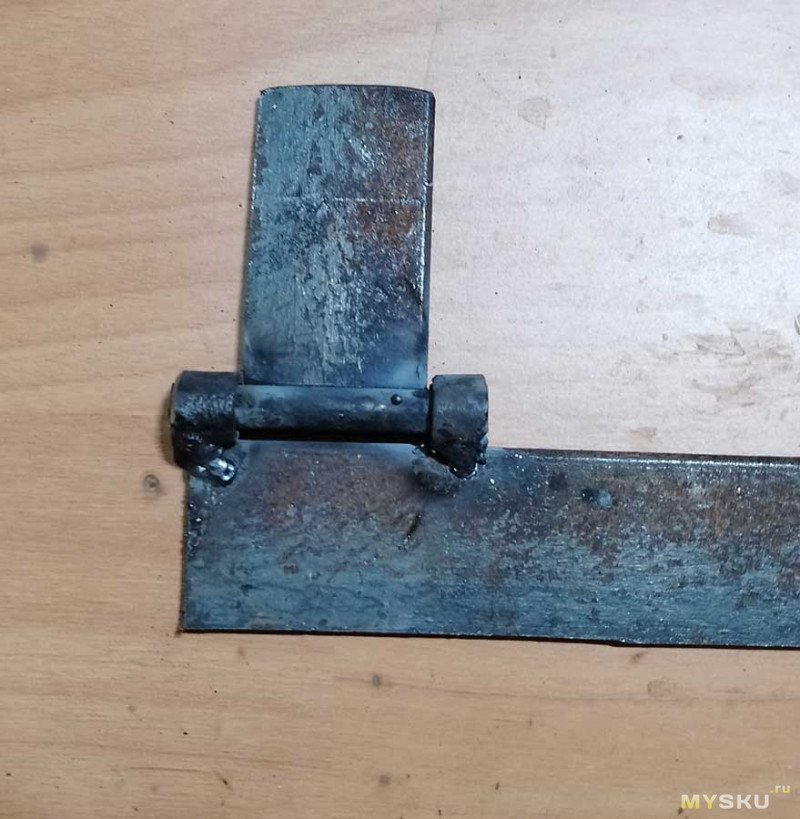
В подвижной части я нарезал резьбу, хотя можно было просто закрепить гайками.
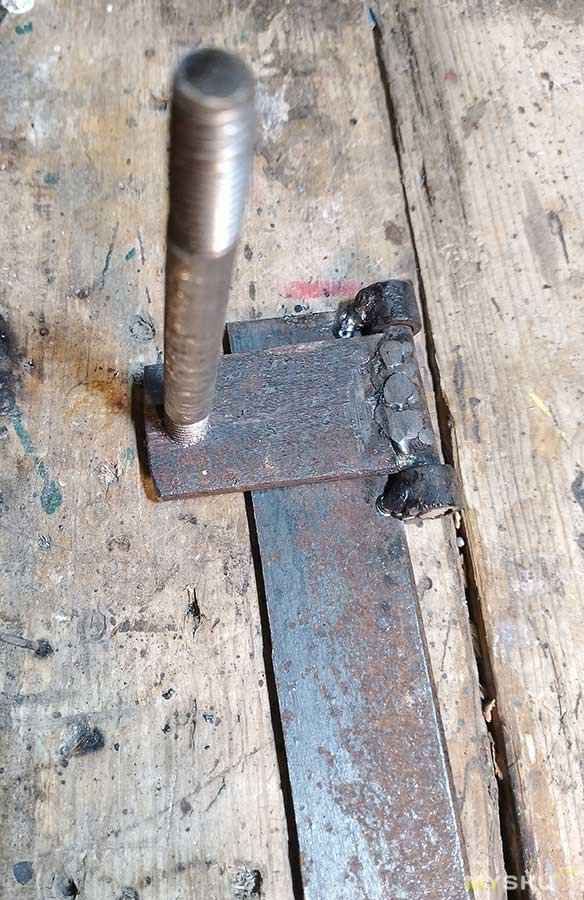
Чуть выше в неподвижной части просверлил отверстие и нарезал резьбу М6. Сюда вкручивается винт, для регулировки.
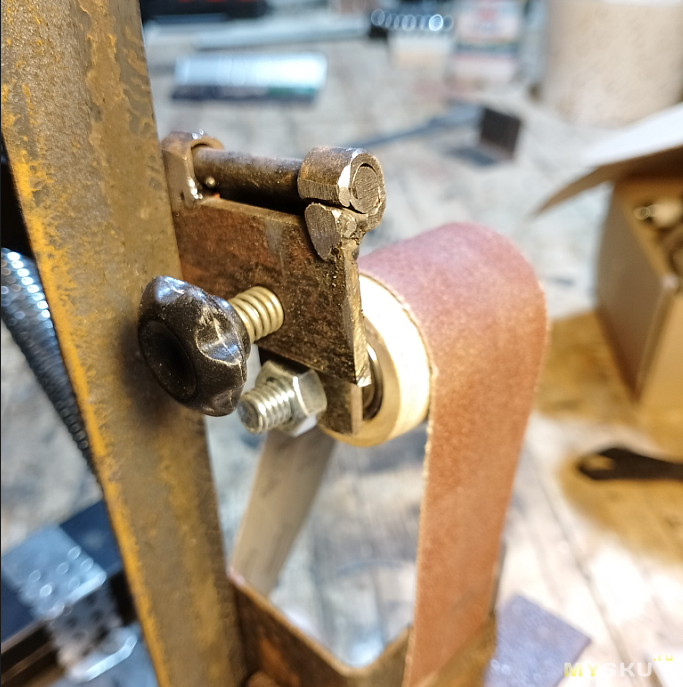
В дальнейшем, пришлось поставить пружину. В противном случае винт потихоньку раскручивался, и лента начинала уходить с роликов.
Закрепив все ролики и надев ленту, нашел примерное место крепления рычага.
На втором конце рычага и в уголке просверлил отверстия, в которые продет кусок пружины диаметром 16 мм, который используется для закрытия дверей и калиток.
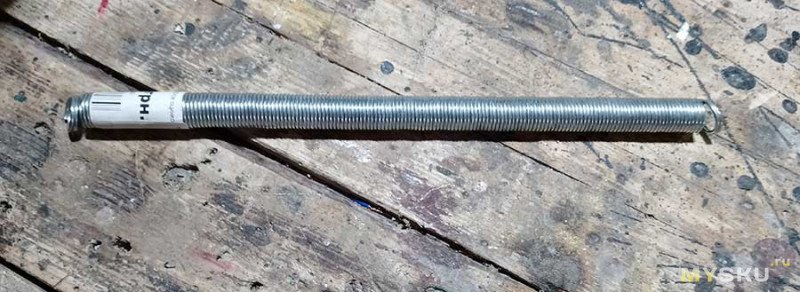
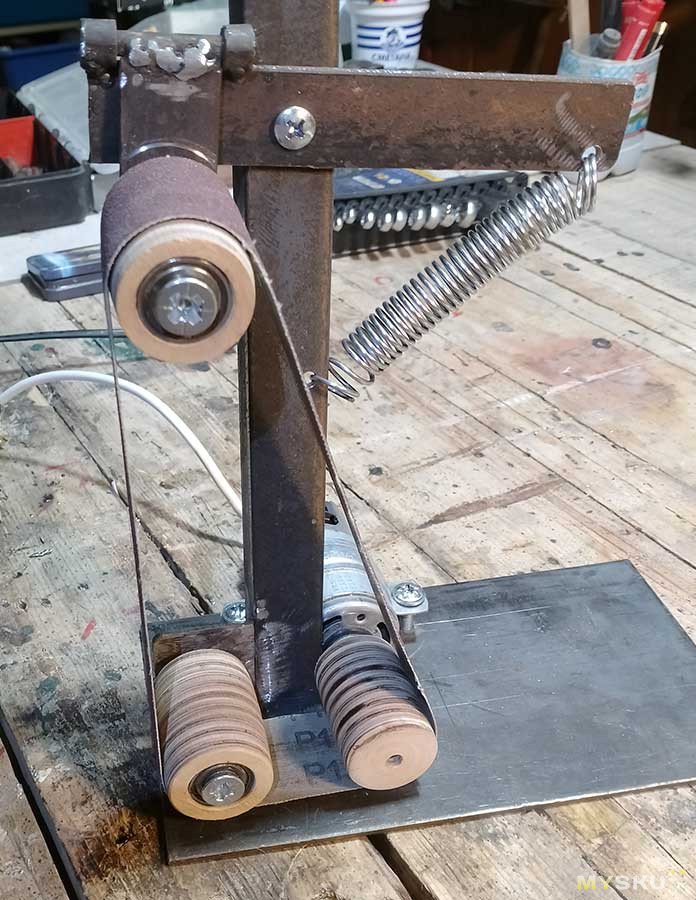
Теперь нужен упор для ленты.
Он был изготовлен из стального листа, толщиной 2 мм и закреплен на уголке с помощью винтов М6.
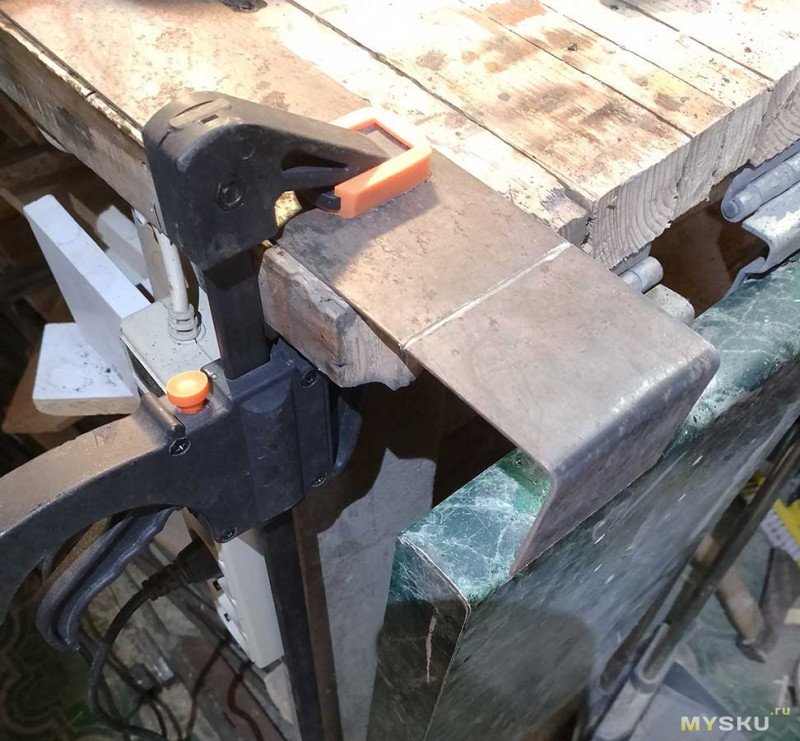
Упорный столик сделан из куска 25 уголка и стальной полосы.
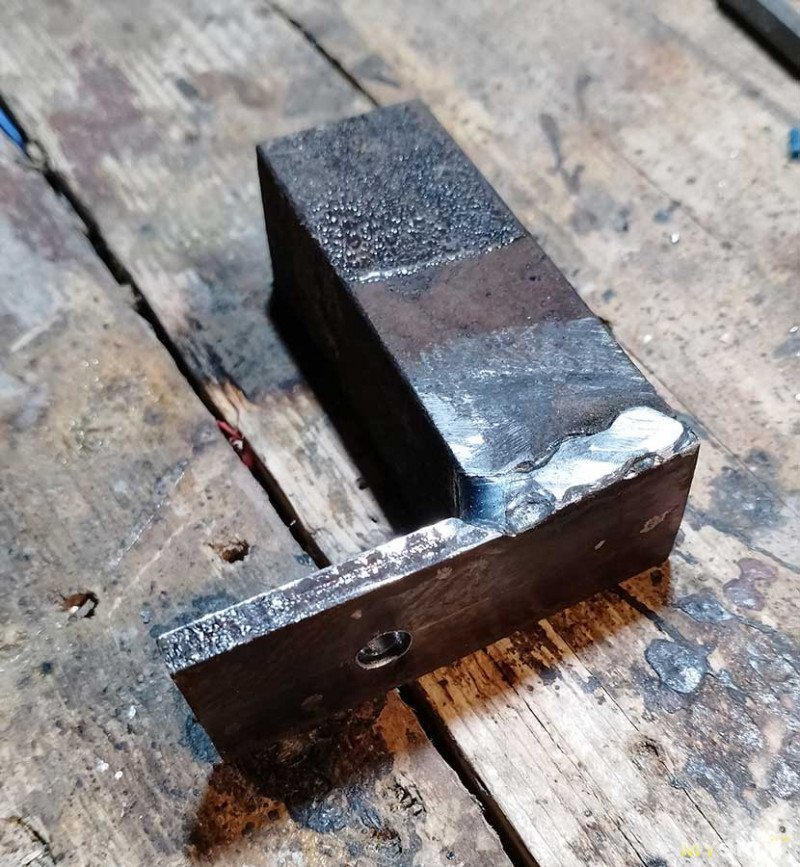
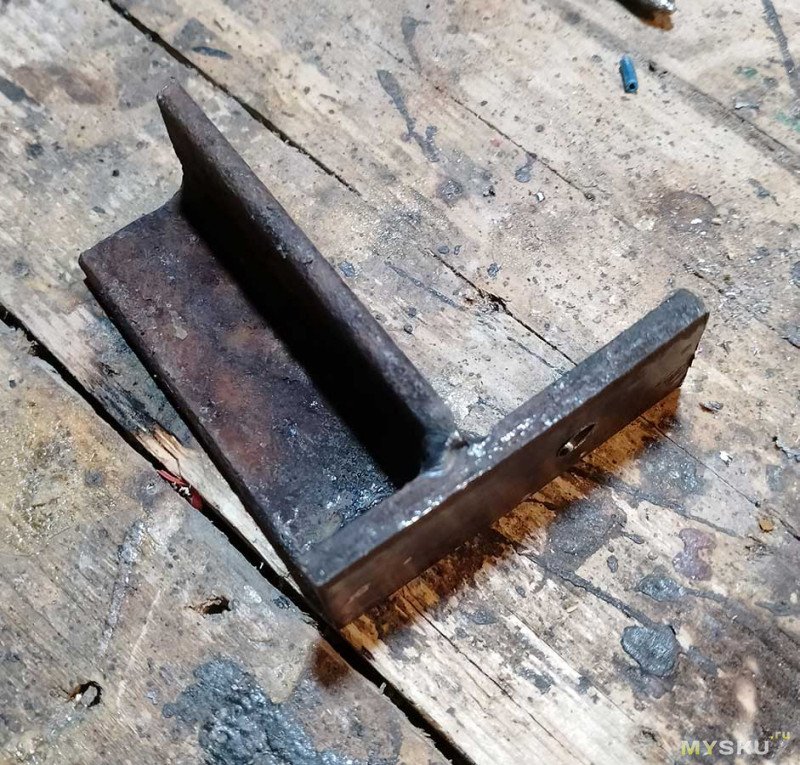
Можно сказать, что все готово, но приключилась неприятность с двигателем.
Дело в том, что направление вращения двигателя блендера по часовой стрелке. Мне же, чтобы лента двигалась вниз, нужно было обратное вращение. Конечно, можно было разместить все части зеркально, т.е. двигатель справа. Но почему-то, практически все гриндеры, как промышленные так и самоделки сделаны по схеме, когда мотор находится слева. Поскольку мотор бленда постоянного тока, то я подумал, что изменить направление вращения будет несложно. Поэтому сделал свой вариант станка по такому же принципу размещения деталей.
Однако, когда я поменял полярность, заметил, что двигатель работает с небольшими перебоями на малой скорости и довольно сильно тянет искру при большой.
Я отнес это к тому, что щетки просто притерлись в одном направлении и со временем проблема уйдет. Разворот щеток на 180 градусов проблему не решил.
В итоге, уже когда весь станок был собран, и на двигатель подалось напряжение, он вдруг отключился через небольшой промежуток времени. Разбор показал, что пластиковый держатель щеток просто расплавился, и щетка впаялась в него. Мало того, в дальнейшем выяснилось, что регулятор тоже вышел из строя.
Уже после этого, когда я ввел в поисковике модель двигателя, совершенно случайно на глаза попался пост на одном из форумов о реверсе этого двигателя. В нем участник рассказывал, что у него возникла точно такая же проблема, как и у меня: при смене направления вращения, двигатель начал тянуть искру. В комментариях кто-то рассказал, что щетки у этого двигателя расположены не по центру ротора, а немного смещены. Поэтому двигатель должен вращаться только по часовой стрелке.
Я уже подумал, что мне предстоит найти новый двигатель, а затем полностью переделать станок, как вспомнил, что у меня есть старый блендер MOULINEX DD 724. Какой оригинальный двигатель там стоял не помню, поскольку много лет назад поменял его на новый, а именно dc781(2)xllg. Он оказался точно такой же мощности и размеров, как и двигатель от Philips.
Как и у предыдущего, направление вращения было по часовой стрелке. Однако, после изменения направления он отлично работал, в отличие от сгоревшего.
В итоге замена двигателя прошла быстро, и ничего переделывать не пришлось.
Еще одной задачей было разместить в каком-нибудь корпусе пусковое устройство для двигателя.
В отличие от Philips в этом не было регулировки скорости, просто две кнопки, которые обеспечивали две скорости работы. Устройство отлично разместилось в корпусе от старого блока питания ноутбука.
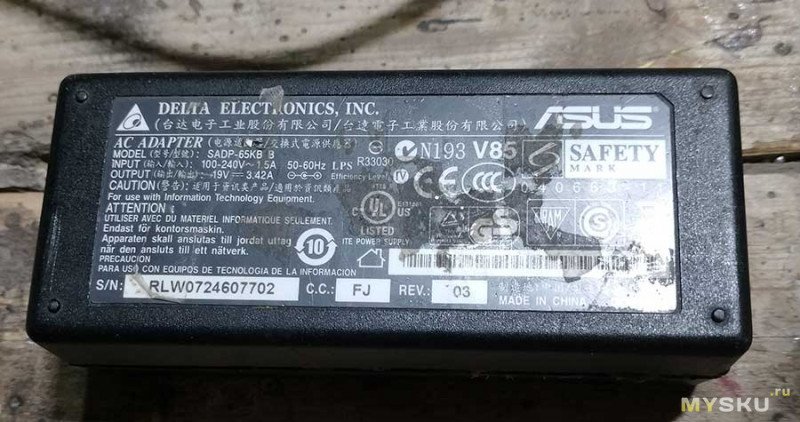
Кнопки были выпаяны, вместо них с торца корпуса установлен трех позиционный выключатель.
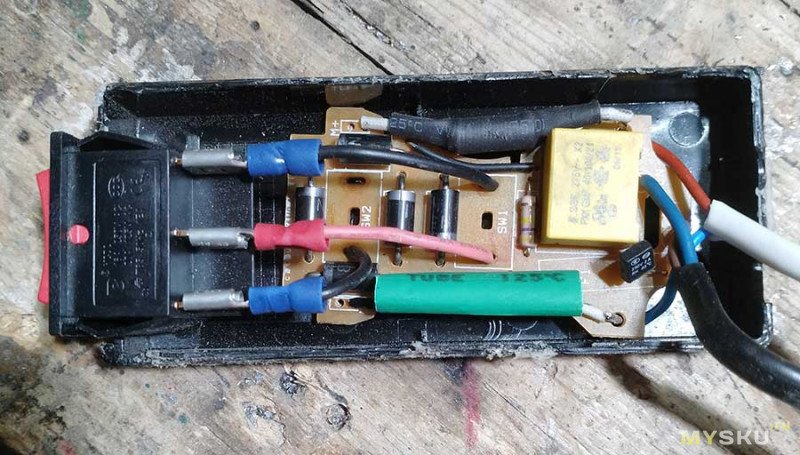
Результат многодневных усилий на фото ниже. Осталось только покрасить.
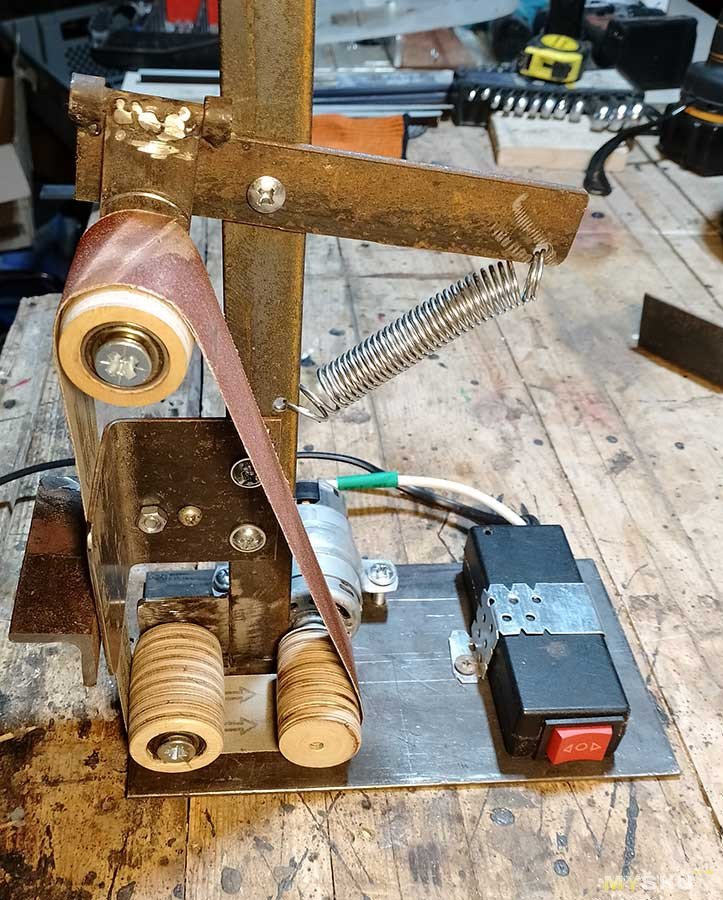
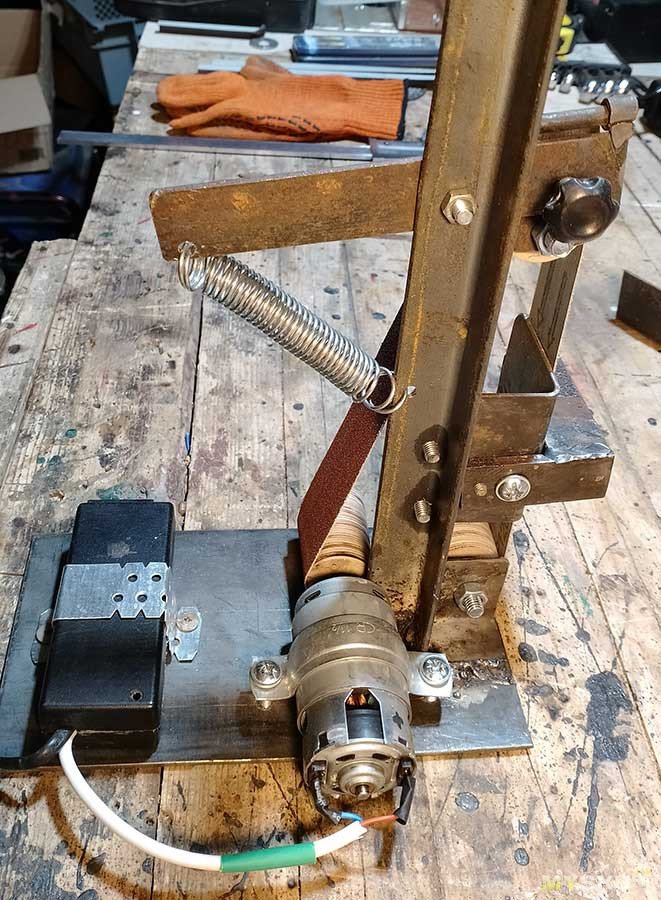
Каков же итог?
Гриндер работает. Довольно удобно затачивать сверла например. Но несмотря на большую мощность двигателя в 700Вт крутящий момент довольно слабый. При более менее сильном нажатии на ленту чувствуется как падает скорость движения. Особенно на малых оборотах. Так что, если нужно точить массивные детали лучше использовать двигатель от стиральной машины или аналогичный.
Как ни старался, но сварка деталей и отсутствие токарного станка дает небольшие погрешности при сборке. В итоге лента не всегда стабильна. Размещение двигателя с помощью хомута отдельно от стойки тоже не лучшая идея. Гораздо функциональнее закрепить все детали на одной вертикальной пластине, как это обычно сделано в промышленных гриндерах.
В этом случае возможно не потребуется бочкообразная форма для роликов. Можно просто использовать набор подшипников.
Еще нужно немного доработать мой вариант, а именно поставить улавливатель для опилок и защитную пластину возле блока питания и над верхним роликом. Хотя я не заметил, что оттуда летит стружка.
Еще в те времена заказал на Али комплект из 10 подшипников 608ZZ: d=8 x D=22 x B=7 mm.
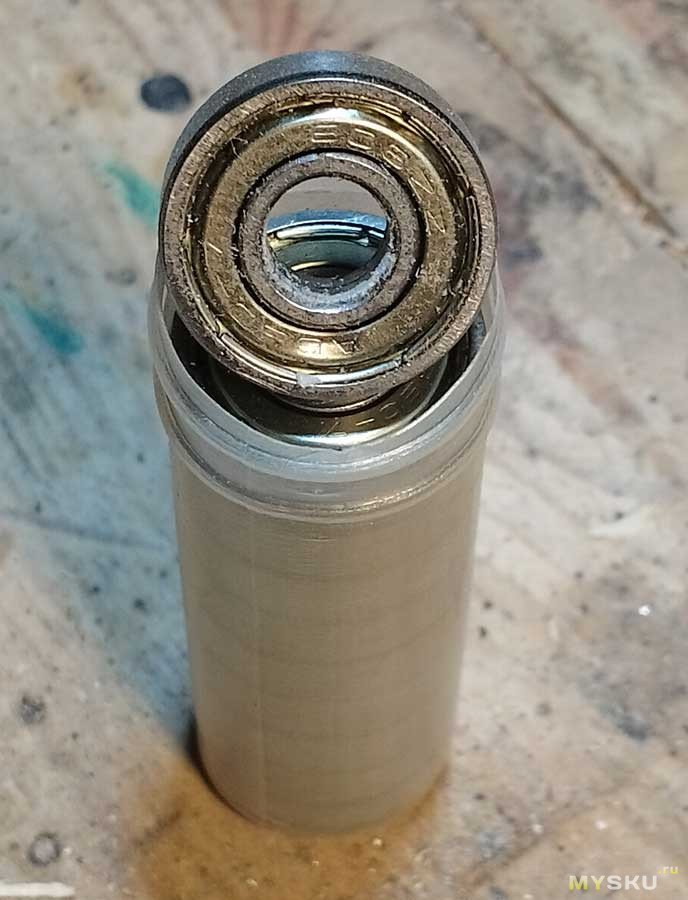
Однако, возможности изготовить тогда у меня не было: ни необходимого инструмента, ни места для изготовления.
Не очень давно, в закромах обнаружился старый электродвигатель от советской стиральной машины, который когда-то выполнял роль точила.
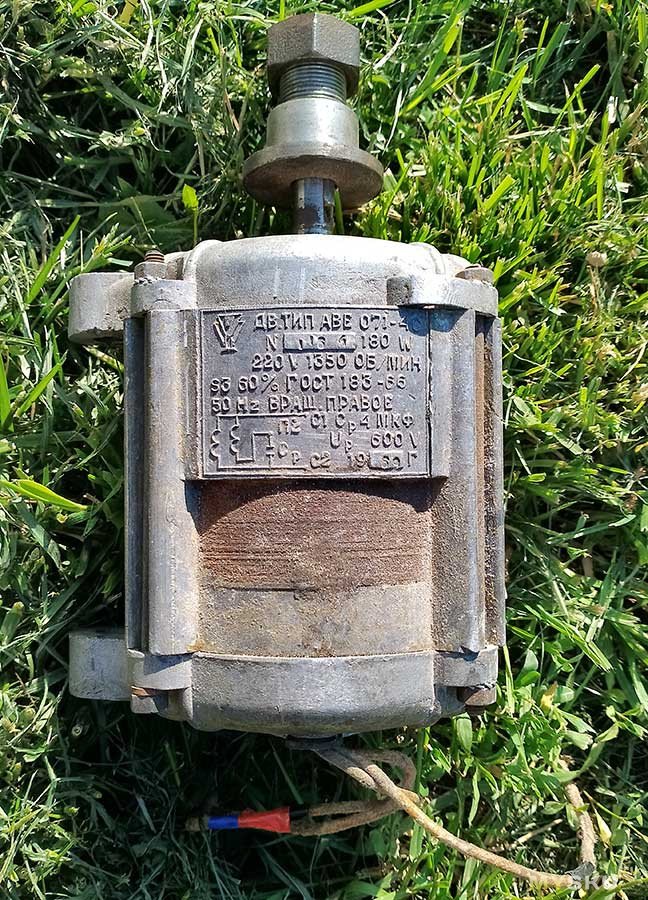
И идея сделать гриндер возникла вновь.
После того, как двигатель был приведен в рабочее состояние, начал просматривать информацию. Вернее выбирать конструкцию из различных самоделок, видео ролики которых есть в интернете.
Параллельно знакомился с теоретической частью.
Для разных материалов требуется разная скорость движения ленты. На рисунке ниже рекомендуемые скорости для разных материалов.
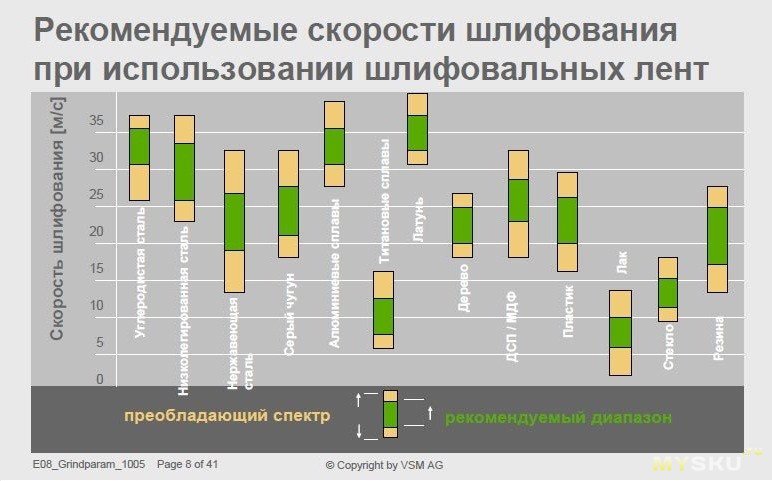
Получалось, что средняя скорость, которая бы подошла для многих примерно 20 м/с.
Исходя из этого параметра нужно было изготовить ведущий ролик, который крепится на вал двигателя.
Не буду утомлять выкладками. Скорость движения ленты рассчитывается по формуле
V = pi * D * n/(60 * 1000), где
V — скорость движения ленты в м/с
D — диаметр ролика в мм
n — количество оборотов двигателя в минуту
pi — известная константа.
Откуда диаметр ролика D = V * 60 * 1000 /(pi * n).
Таким образом, чтобы достичь необходимой скорости ленты для этого двигателя понадобится ролик диаметром 20*60000/(3,14*1350) = 283 мм.
Мне показалось, что он несколько великоват.
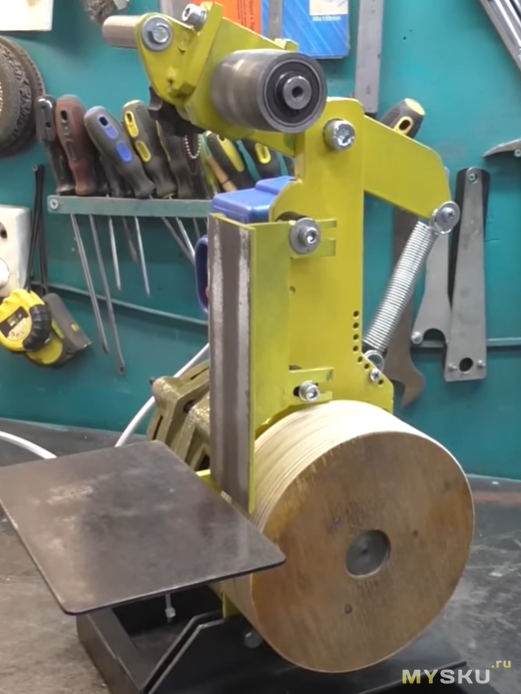
Однако идея изготовить станок уже поселилась в моей голове, и я стал искать другие варианты.
Среди объявлений на OLX обнаружил продажу б/у двигателей от разных современных стиральных машин. Стоимость такого двигателя примерно $10.
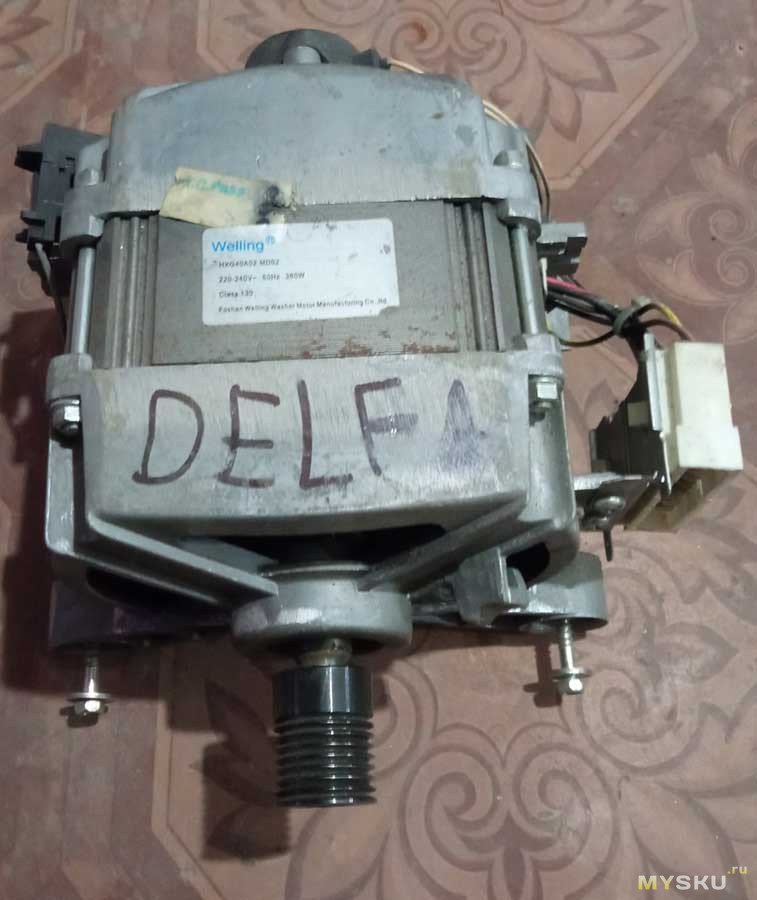
Максимальная скорость вращения 13000-16000 оборотов в минуту.
Таким образом, диаметр ролика мог быть порядка 30 мм.
Еще одним плюсом было то, что на Али есть масса предложений регуляторов оборотов для таких двигателей.
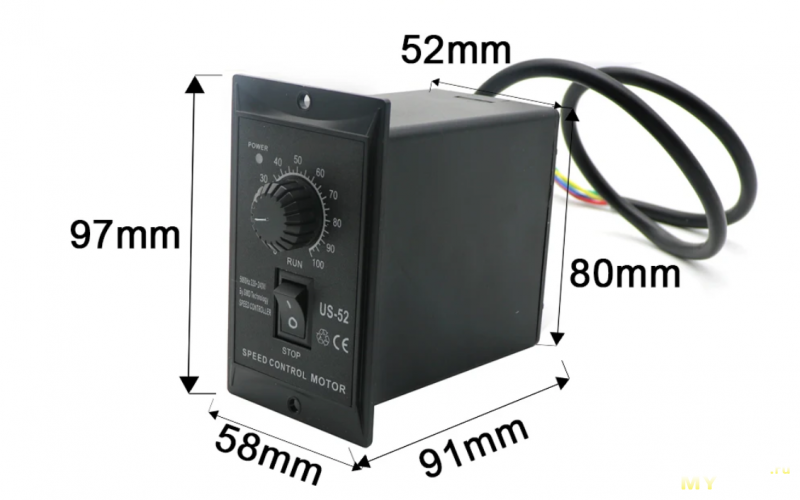
На OLX было много предложений бесколлекторных или индукционных двигателей. Однако, я так и не нашел устройства, с помощью которого такой двигатель можно было включить.
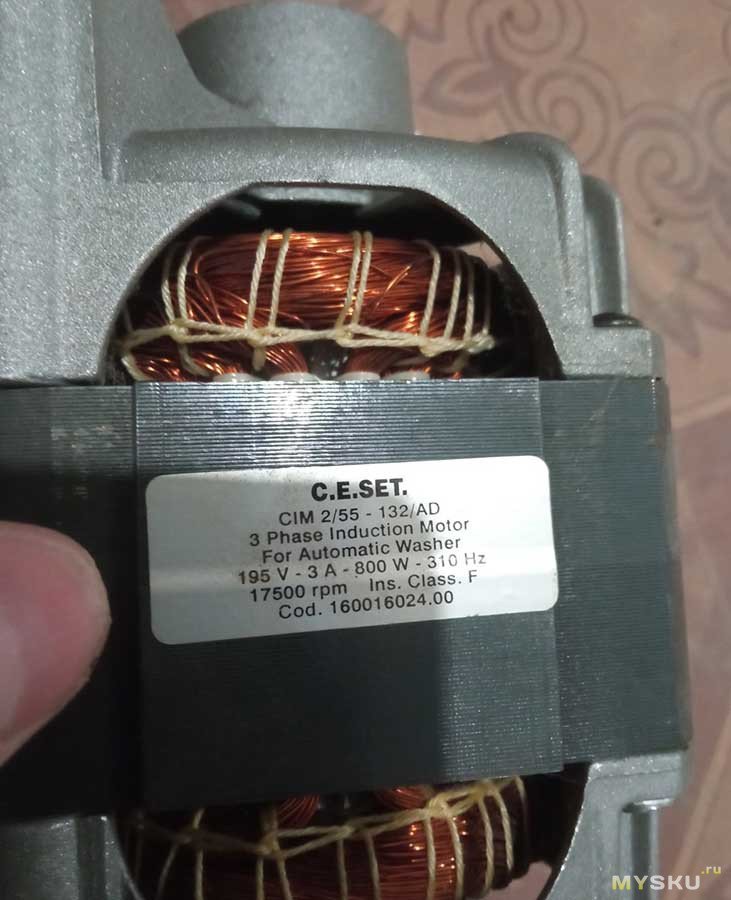
Но тут я подумал, а зачем мне такой громоздкий агрегат на рабочем столе? Пользоваться я буду им не очень часто, даже пока не знаю где можно его применить. Может заточка сверл, ножей или еще чего.
Более миниатюрный вариант можно изготовить из двигателя от шуруповерта, например.
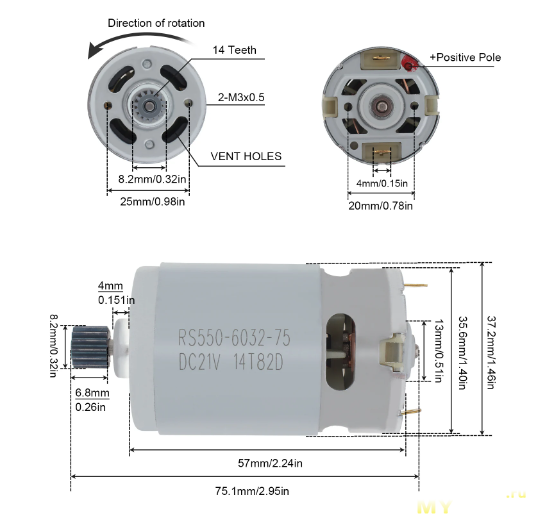
Однако, мощность такого двигателя довольно маленькая порядка 90-100Вт.
И тут на глаза попался моторный блок от старого блендера. Правда, мощность именно этого варианта была тоже не очень большой — 300Вт.
На том же OLX можно найти много предложений моторных блоков или даже блендеров с поломанными чашами или другими частями ценой от $5.
Но мне повезло еще больше. В разговоре один из знакомых сказал, что у него валяется такой моторный блок, и он с удовольствием его мне отдаст.
Это оказался блок от блендера Philips HR1372.
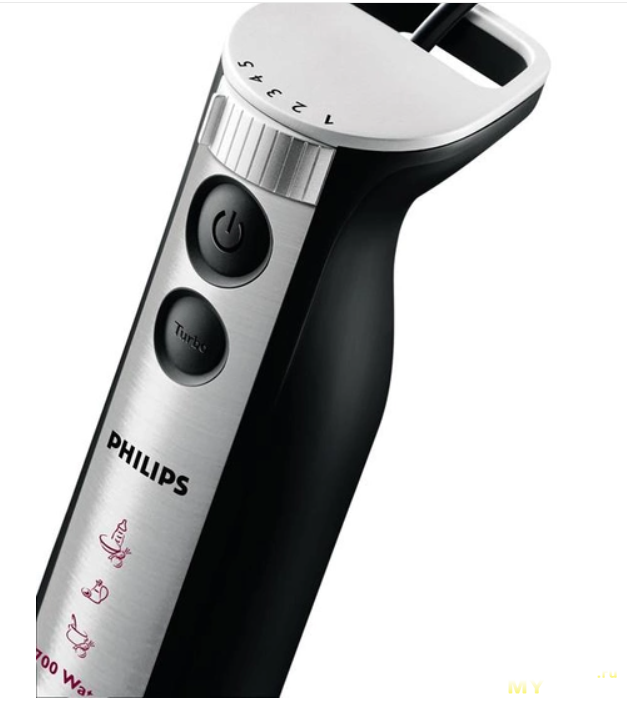
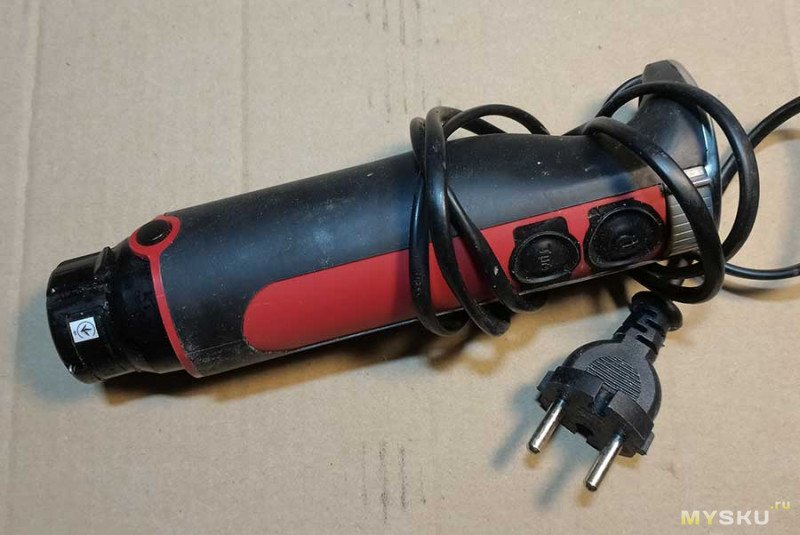
Внутри двигатель WRS-7912PM. Мощность 700Вт. Небольшие размеры еще и регулятор оборотов в наличии. Идеальный вариант.
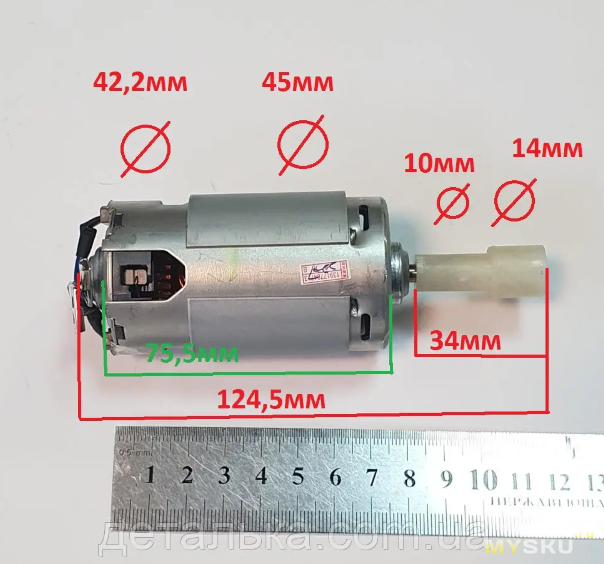
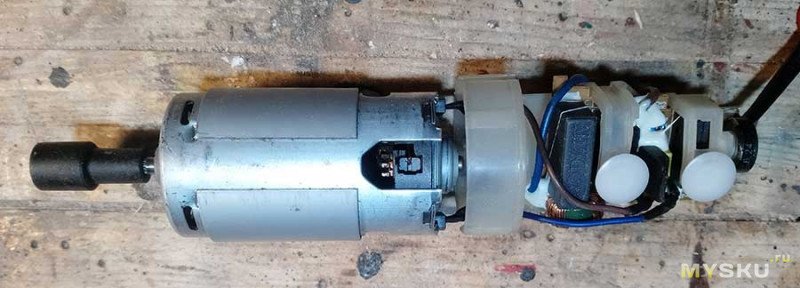
Однако, мне никак не удавалось найти информацию о скорости вращения.
ИИ любезно сообщил, что скорость оборотов бытовых блендеров примерно 10000 оборотов в минуту. Что в общем тоже отлично подойдет для гриндера.
Но мне хотелось точнее узнать скорость конкретного двигателя. И опять поиски в интернете. Вариантов как определить скорость довольно много. Но в основном они подходят для трехфазных двигателей с небольшим количеством оборотов, порядка 1000.
Наконец мне удалось найти отличный способ. Идея состоит в том, что на вал двигателя крепится небольшой неодимовый магнит. Я отломал кусок от магнита из HDD. Далее необходим тестер, умеющий измерять частоту. Такой тоже у меня нашелся, который был приобретен не так давно.
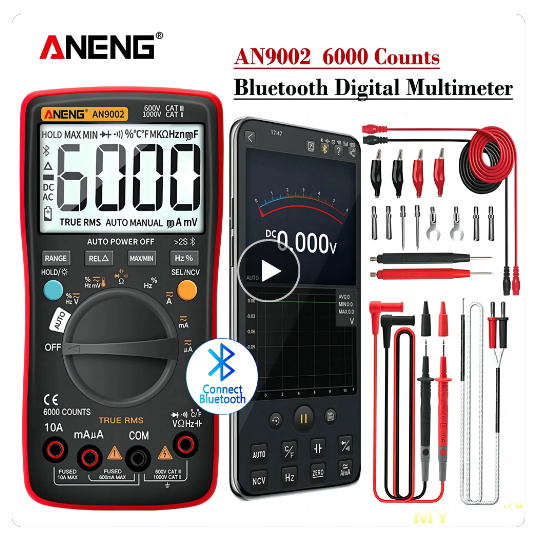
К щупам подключается любая катушка. На сколько я понимаю, чем больше витков будет, тем лучше. Я выпаял небольшой трансформатор с платы телевизора и вытащил из него сердечник.
Двигатель включается, катушка подносится к вращающемуся валу. На тестере возникает частота в герцах (количество колебаний в секунду). Умножив ее на 60 получаем количество оборотов в минуту.
Измерения показали, что максимальные обороты двигателя 12000 обр.мин, а минимальные — 8200.
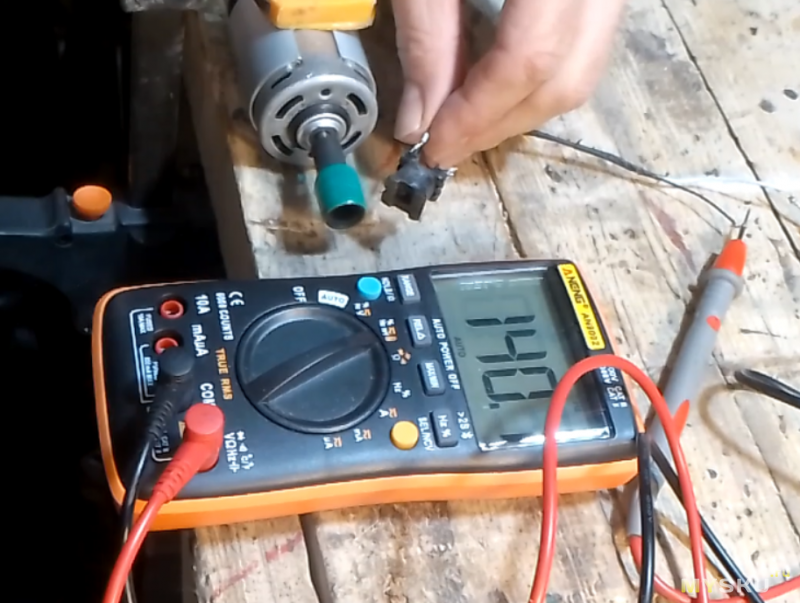
Для гриндера решил использовать ленту для шлифовальной машины длиной 533 мм и шириной 75 мм (по словам продавца самая популярная). 75 мм слишком широкая для такого двигателя, поэтому ленту разорвал пополам.
Следующим шагом было изготовить ведущий и пассивные ролики. Исходя из ширины ленты и оборотов двигателя ролик должен быть примерно 31 мм в диаметре и шириной 40 мм. На многих видео авторы рекомендуют использовать муфты бочкообразной формы. Это стабилизирует ленту.
Доступа к токарному станку у меня нет. Но в интернете полно идей как изготовить ролики без токарного станка.
Первая идея, это использовать соединительные муфты для пайки полипропиленовых труб. С муфтой для трубы 32 мм отлично подходят подшипники диаметром 32 мм. Внешний диаметр такой муфты 45 мм, а длина 40. Почти то что нужно. Кроме того, такие муфты уже есть бочкообразной формы.
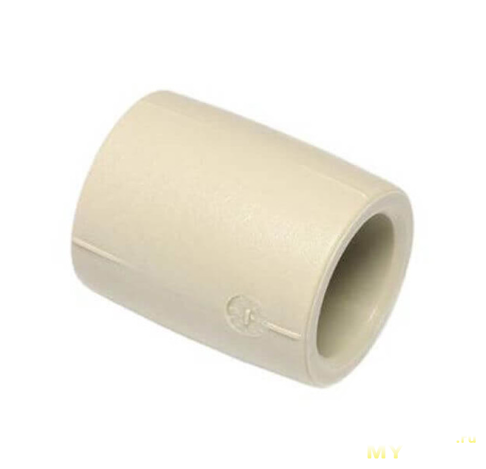
Но у меня в наличии подшипники диаметром 22 мм.
В закромах нашелся кусок трубы PN 20. Внешний диаметр 32 мм. То что доктор прописал.
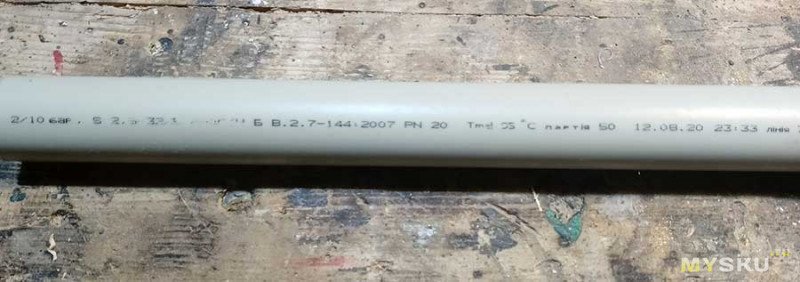
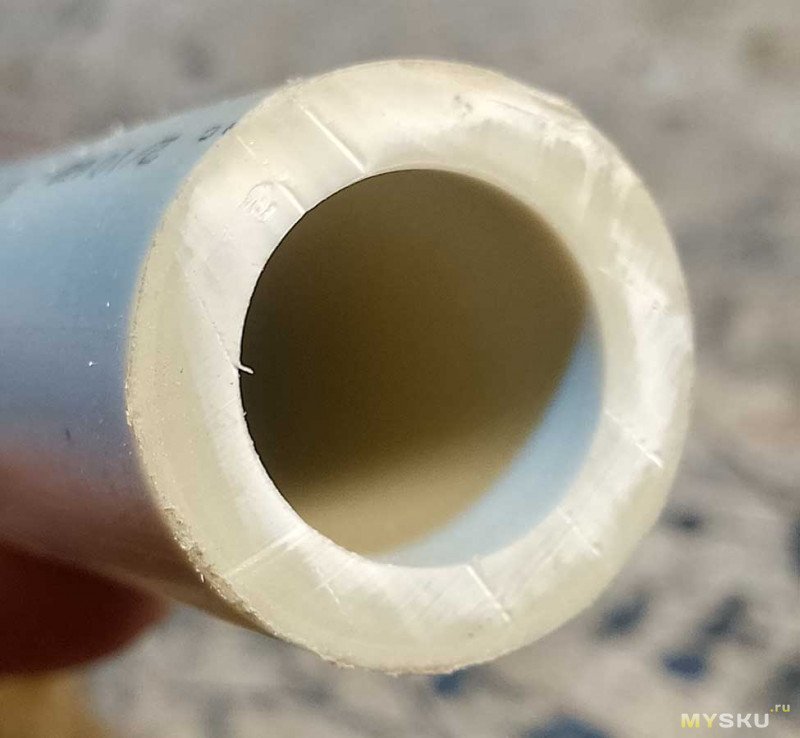
Были отрезаны два куска трубы, а также вставки из металлической трубки, чтобы подшипники не заклинило при затягивании на оси.
Подшипники легко запрессовались с помощью тисков. Но при этом труба расширилась в местах запрессовки.
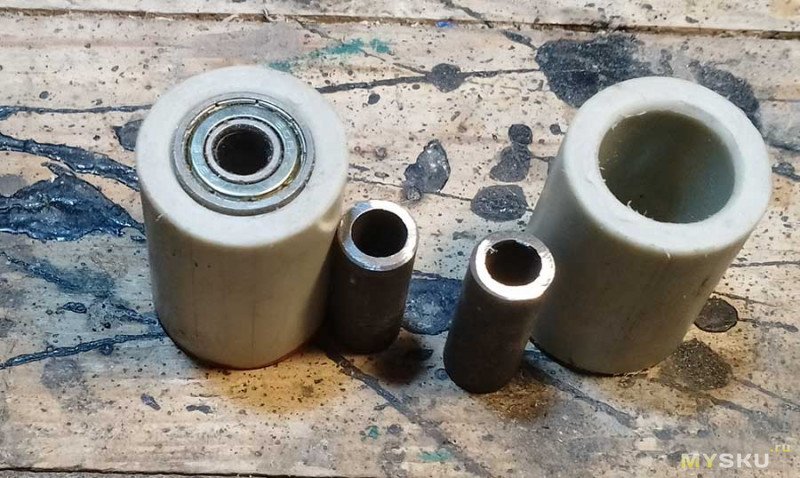
Но как я ни старался отрезать ровно полипропиленовую и металлическую трубы, мне это не удалось. В результате даже расхождения в пару миллиметров вызвало перекос подшипников относительно оси. Опять же, токарный станок в этом случае помог бы.
Следующей идеей было изготовить ролики из фанеры, вырезав из нее круги нужного диаметра и склеив друг с другом. В дрель была закреплена коронка для проделывания отверстий в гипсокартоне.
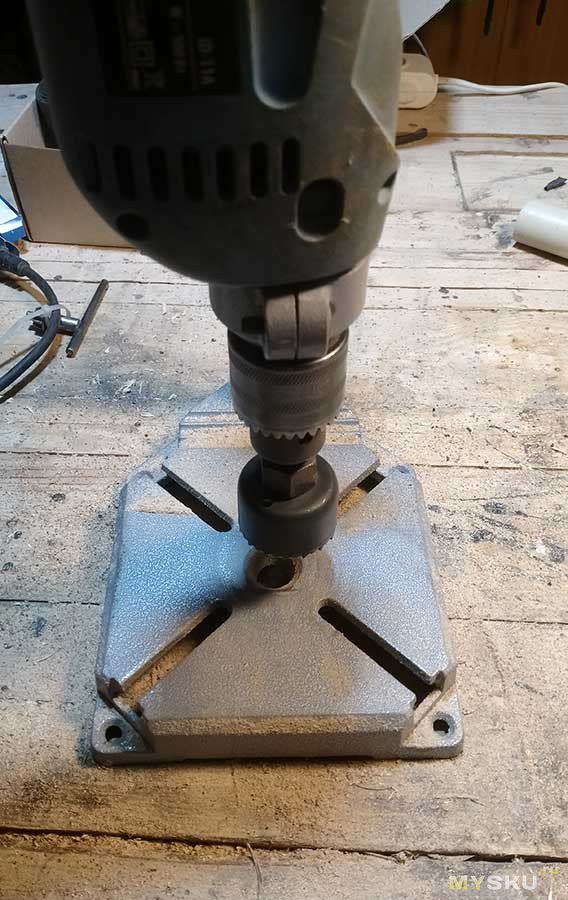
Как ни странно, она довольно легко справилась с поставленной задачей.
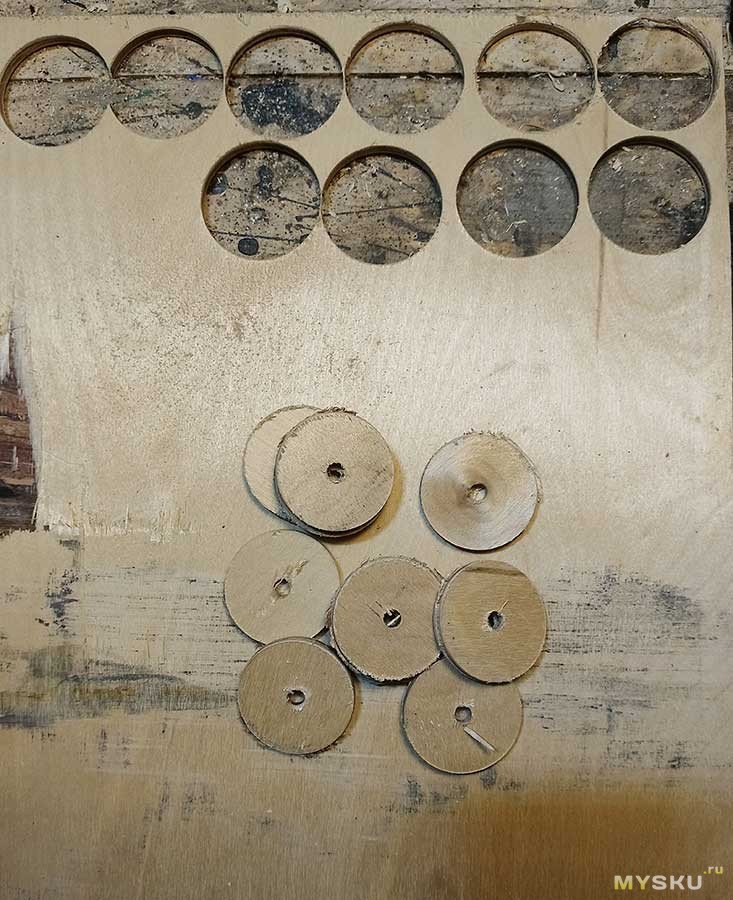
Затем круги последовательно одеваются на болт подходящего диаметра, каждый слой промазывается клеем (ПВА подходит) и этот слоенный пирог сжимается с помощью гаек и струбцин.
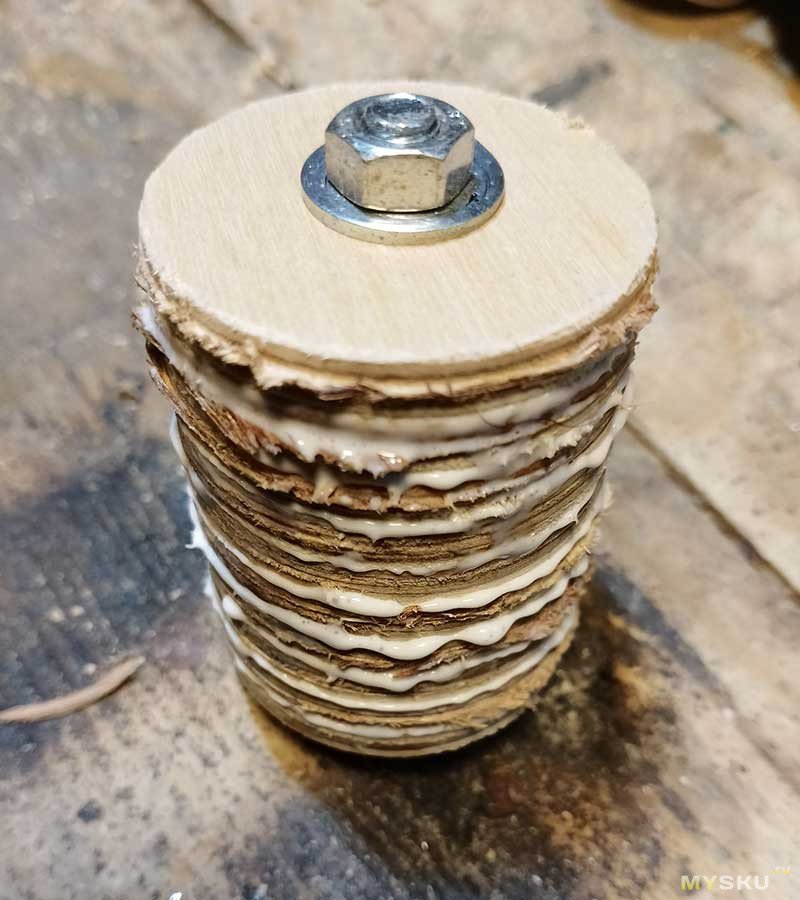
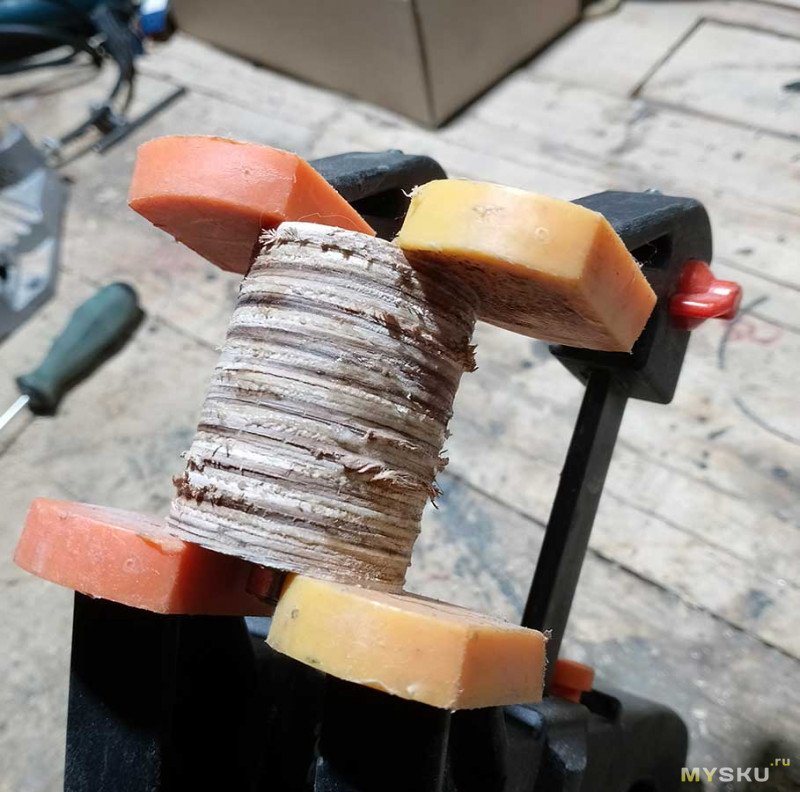
Лайвхак. Диаметр отверстия посередине круга примерно 6 мм. Желательно сразу рассверлить его до необходимого, в моем случае до 10мм, потому что внутренний диаметр подшипника 8 мм. Точно увеличить отверстие в уже готовом ролике намного сложнее и не всегда получается. Я испортил один таким образом.
После высыхания клея, оказалось, что болт плотно сидит внутри ролика и извлечь его можно только выкрутив. Эта особенность сослужила мне хорошую службу.
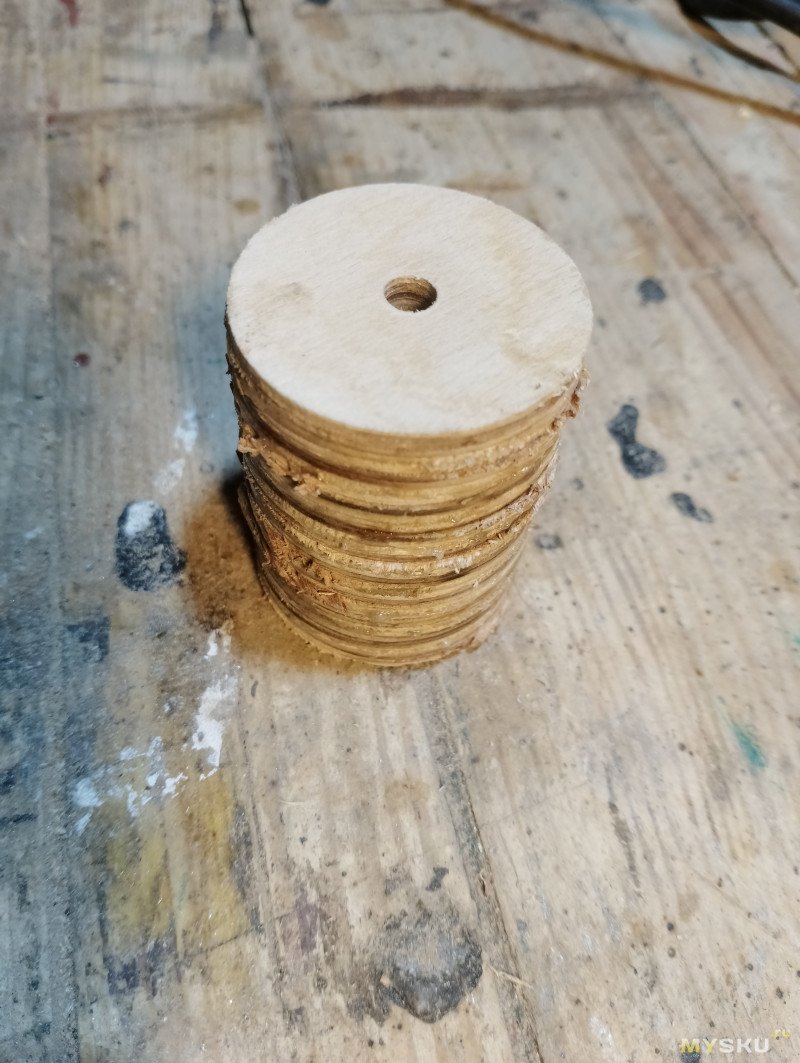
Диаметр склеенного ролика примерно 40 мм.
Но края ролика крайне неровные, а токарного станка нет.
Для дальнейшей обработки можно использовать обычную дрель. Стержень выкручивается из ролика таким образом, чтобы с одного края оставалось место на толщину подшипника плюс небольшой запас. За счет того, что стержень имеет резьбу, дополнительного крепления ролика не требуется.
Направление вращения дрели выбирается таким образом, чтобы ролик накручивался на стержень, т.е. против часовой стрелки.
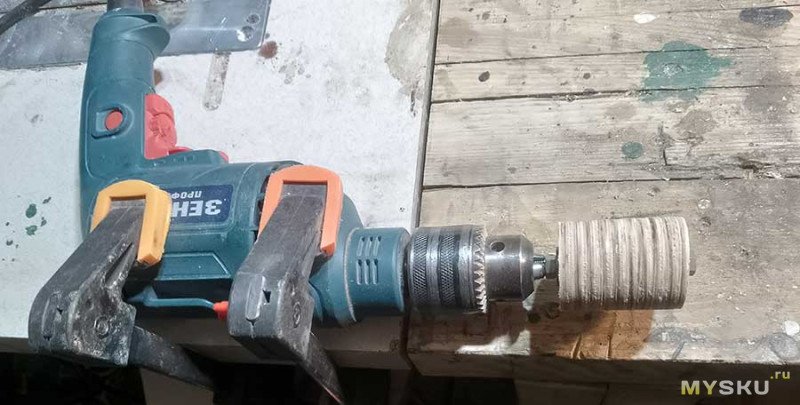
Далее идет обработка ролика как на токарном станке. Для обработки можно использовать например стамеску. Но мне больше понравилось обтачивать с помощью болгарки и шлифовального диска.
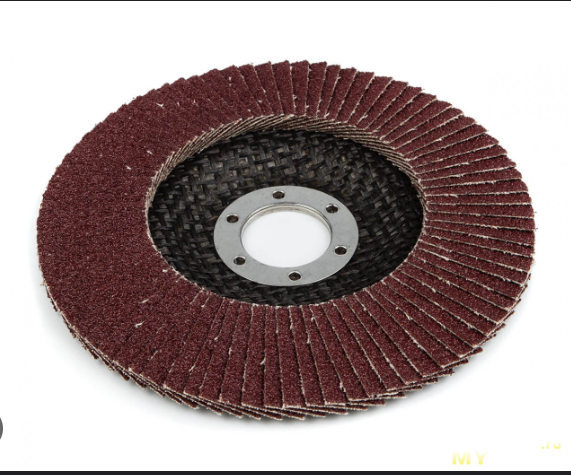
Опять же, направления вращения дрели и круга болгарки должны быть противоположными.
Таким образом ролик довольно быстро принимает нужную форму и гладкую поверхность.
В итоге получился ролик диаметром примерно 31 мм бочкообразной формы.
На двигателе есть пластиковая муфта диаметрами 10 и 14 мм.
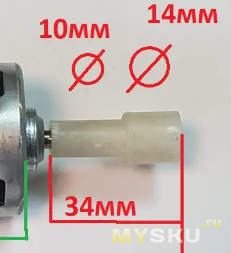
Более толстая часть была срезана. В одном из роликов было просверлено отверстие чуть меньше 10мм и ролик был посажен на клей.
Для остальных роликов нужно было изготовить посадочное место для подшипников.
Это делается с помощью все той же стамески на валу дрели.
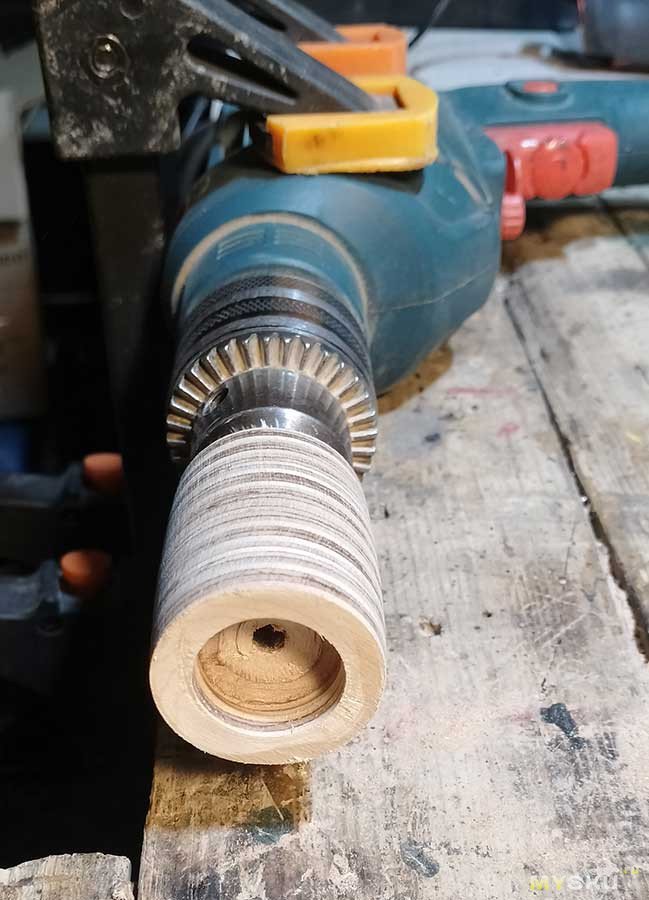
При постоянной примерке удалось достаточно точно изготовить посадочные места. Даже не вклеивал подшипники, а просто запрессовал.
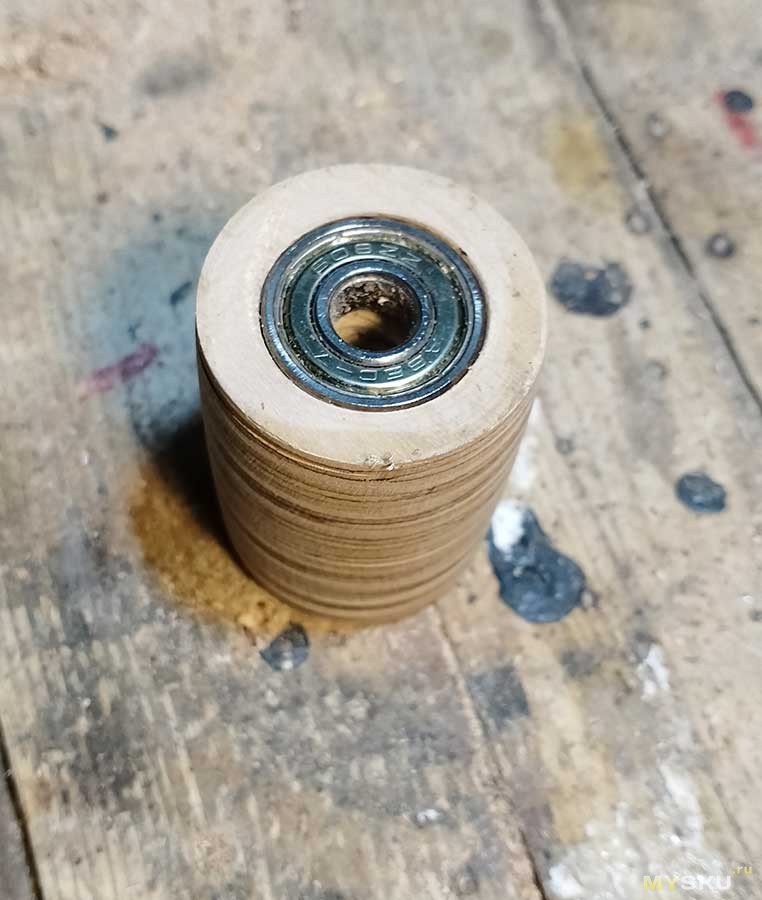
Далее нужно было изготовить собственно станину, на которой будут крепиться ролики и двигатель.
На пункте приема металлолома была приобретена металлическая пластина 220*120 мм и толщиной 3,5 мм.
К ней был приварен уголок 25 мм и внизу небольшой кусочек пластины для крепления нижнего ролика.
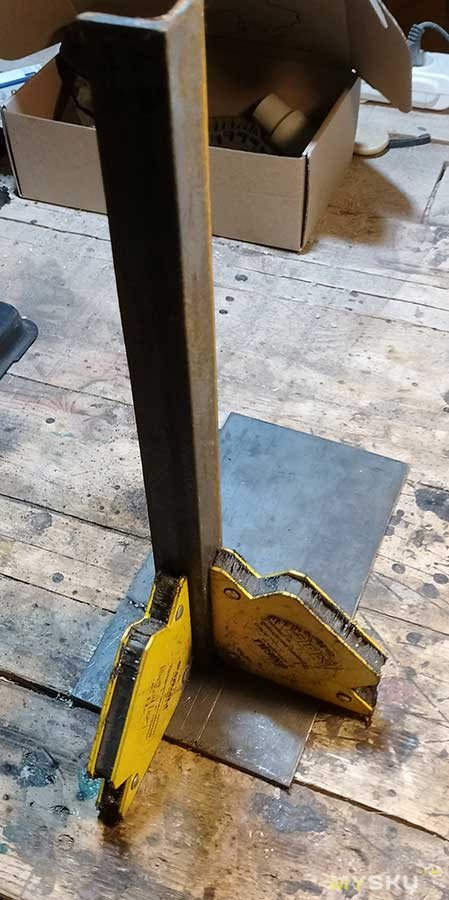
Двигатель был закреплен рядом с уголком с помощью хомута.
Далее нужно было сделать рычаг для верхнего ролика. Этот ролик должен быть подвижным, чтобы можно было натягивать ленту.
Рычаг изготовлен из куска стальной полосы шириной 25 мм и толщиной 3,5 мм Кроме того, ось верхнего ролика должена смещаться от горизонтального положения. Это необходимо чтобы регулировать ленту, когда она пытается уйти с роликов.
Сначала я приварил старую оконную петлю. Но это оказалось неудачным решением. Она довольно сильно выступала в сторону, кроме того, вал ролика нельзя было закрепить с помощью гайки. Пришлось делать навес самостоятельно.
Два небольших отрезка трубы в качестве петель. К куску все той же полосы приварен отрезок катанки подходящего диаметра. После того, как все это выставляется, отрезки трубки привариваются к полосе.
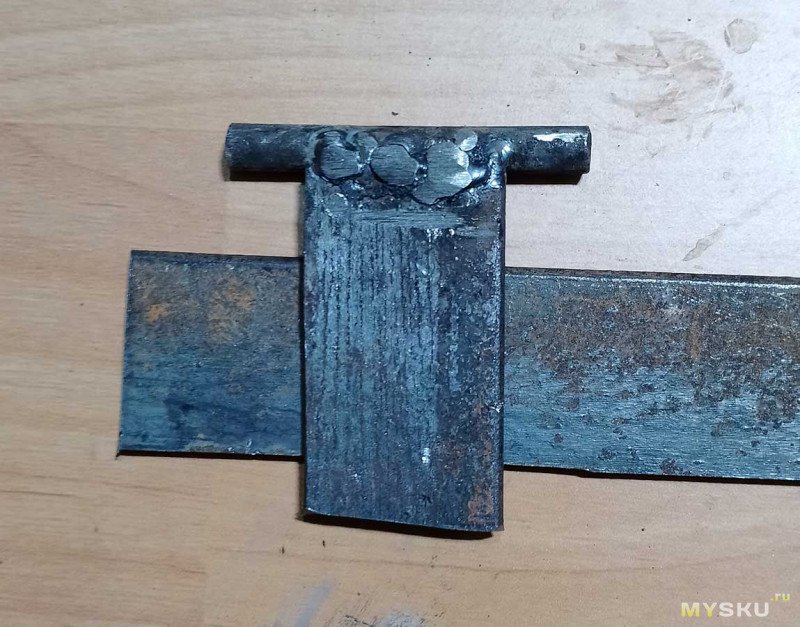
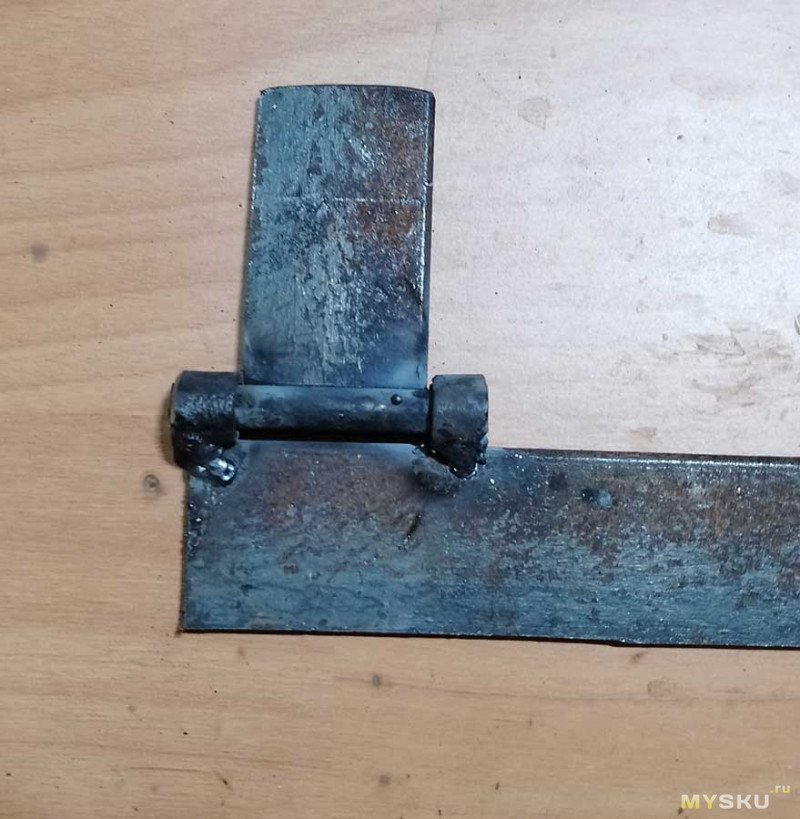
В подвижной части я нарезал резьбу, хотя можно было просто закрепить гайками.
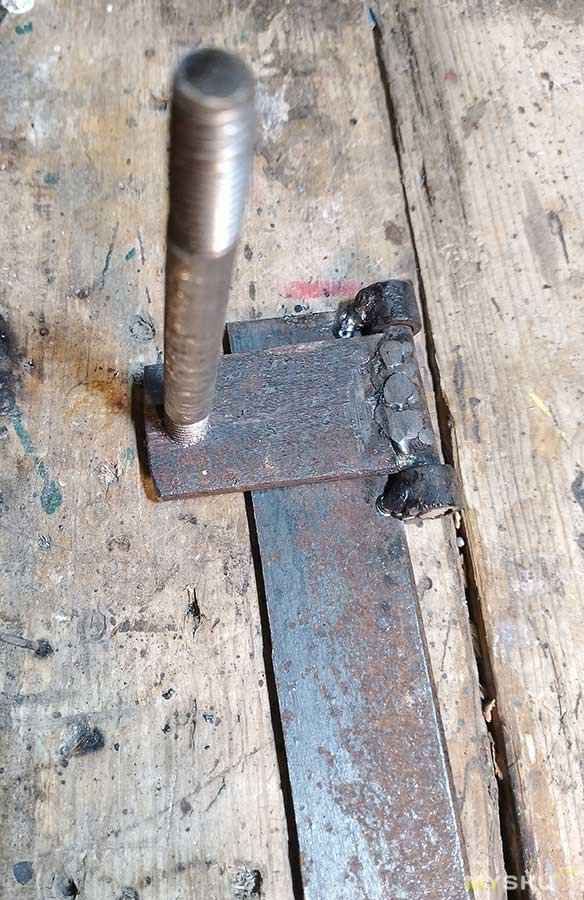
Чуть выше в неподвижной части просверлил отверстие и нарезал резьбу М6. Сюда вкручивается винт, для регулировки.
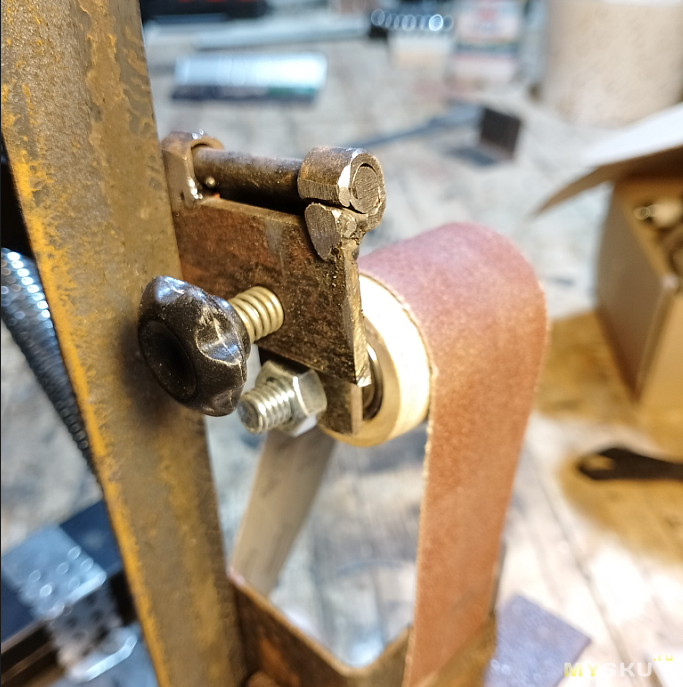
В дальнейшем, пришлось поставить пружину. В противном случае винт потихоньку раскручивался, и лента начинала уходить с роликов.
Закрепив все ролики и надев ленту, нашел примерное место крепления рычага.
На втором конце рычага и в уголке просверлил отверстия, в которые продет кусок пружины диаметром 16 мм, который используется для закрытия дверей и калиток.
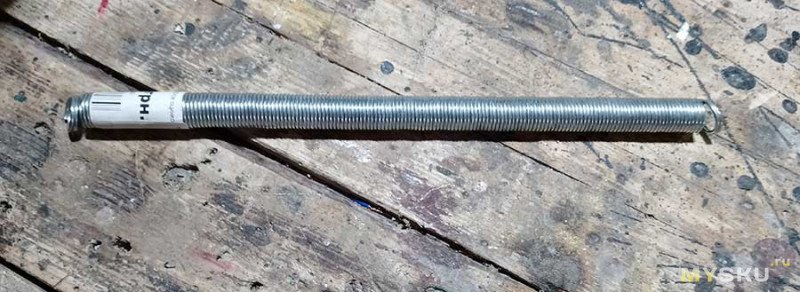
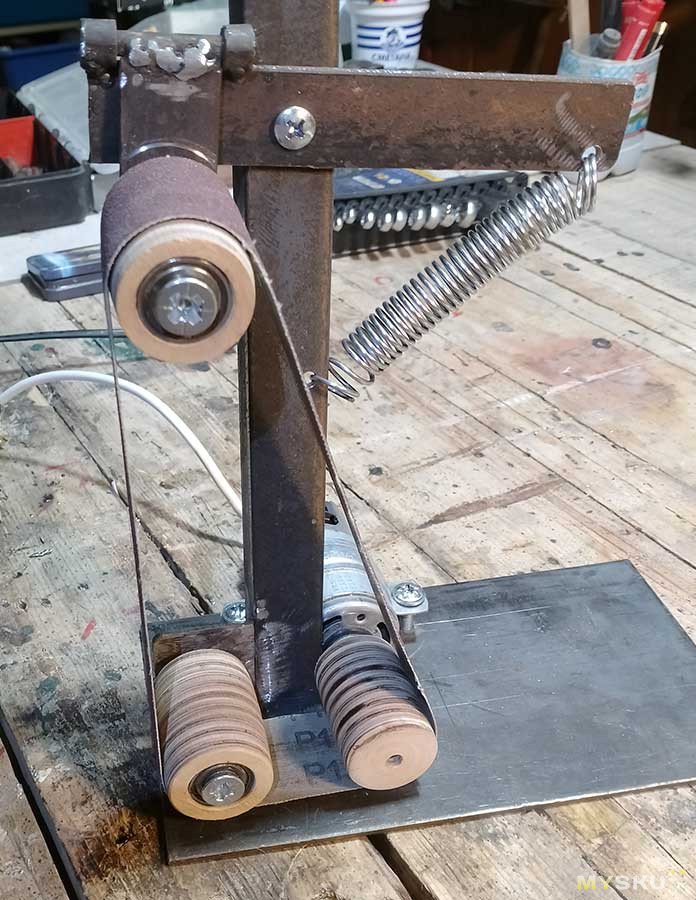
Теперь нужен упор для ленты.
Он был изготовлен из стального листа, толщиной 2 мм и закреплен на уголке с помощью винтов М6.
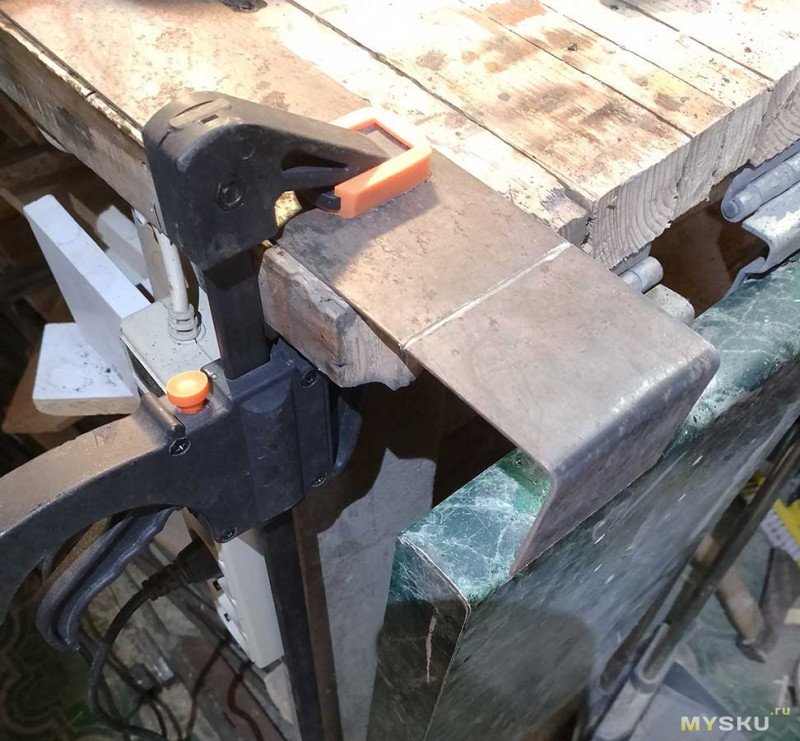
Упорный столик сделан из куска 25 уголка и стальной полосы.
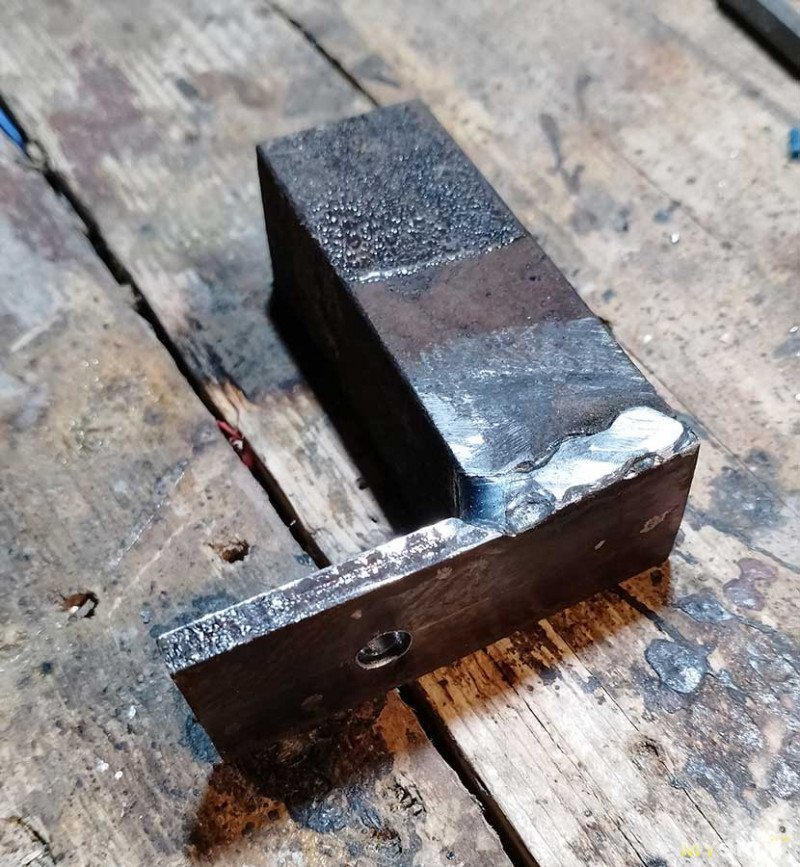
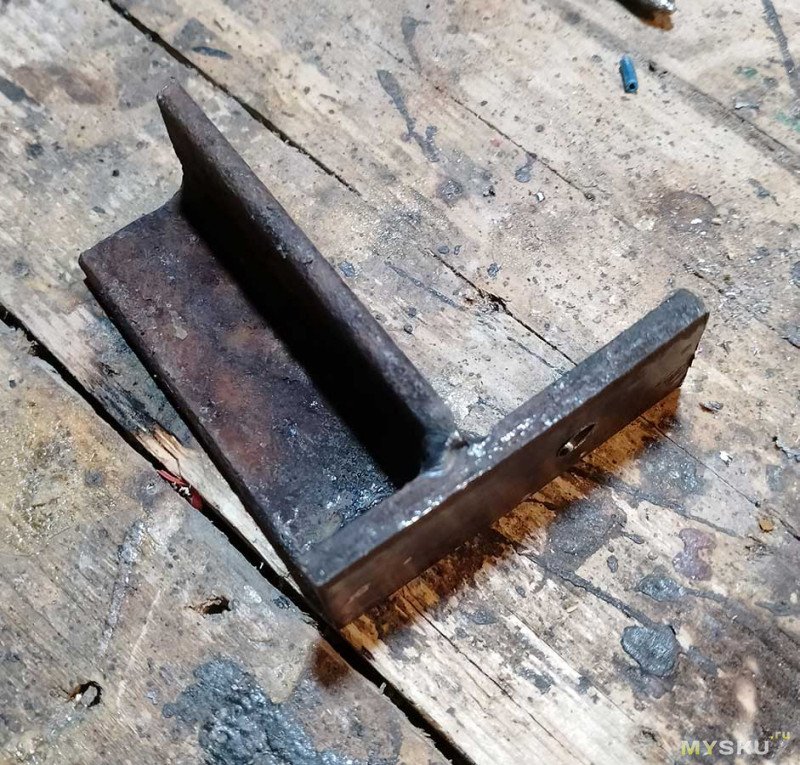
Можно сказать, что все готово, но приключилась неприятность с двигателем.
Дело в том, что направление вращения двигателя блендера по часовой стрелке. Мне же, чтобы лента двигалась вниз, нужно было обратное вращение. Конечно, можно было разместить все части зеркально, т.е. двигатель справа. Но почему-то, практически все гриндеры, как промышленные так и самоделки сделаны по схеме, когда мотор находится слева. Поскольку мотор бленда постоянного тока, то я подумал, что изменить направление вращения будет несложно. Поэтому сделал свой вариант станка по такому же принципу размещения деталей.
Однако, когда я поменял полярность, заметил, что двигатель работает с небольшими перебоями на малой скорости и довольно сильно тянет искру при большой.
Я отнес это к тому, что щетки просто притерлись в одном направлении и со временем проблема уйдет. Разворот щеток на 180 градусов проблему не решил.
В итоге, уже когда весь станок был собран, и на двигатель подалось напряжение, он вдруг отключился через небольшой промежуток времени. Разбор показал, что пластиковый держатель щеток просто расплавился, и щетка впаялась в него. Мало того, в дальнейшем выяснилось, что регулятор тоже вышел из строя.
Уже после этого, когда я ввел в поисковике модель двигателя, совершенно случайно на глаза попался пост на одном из форумов о реверсе этого двигателя. В нем участник рассказывал, что у него возникла точно такая же проблема, как и у меня: при смене направления вращения, двигатель начал тянуть искру. В комментариях кто-то рассказал, что щетки у этого двигателя расположены не по центру ротора, а немного смещены. Поэтому двигатель должен вращаться только по часовой стрелке.
Я уже подумал, что мне предстоит найти новый двигатель, а затем полностью переделать станок, как вспомнил, что у меня есть старый блендер MOULINEX DD 724. Какой оригинальный двигатель там стоял не помню, поскольку много лет назад поменял его на новый, а именно dc781(2)xllg. Он оказался точно такой же мощности и размеров, как и двигатель от Philips.
Как и у предыдущего, направление вращения было по часовой стрелке. Однако, после изменения направления он отлично работал, в отличие от сгоревшего.
В итоге замена двигателя прошла быстро, и ничего переделывать не пришлось.
Еще одной задачей было разместить в каком-нибудь корпусе пусковое устройство для двигателя.
В отличие от Philips в этом не было регулировки скорости, просто две кнопки, которые обеспечивали две скорости работы. Устройство отлично разместилось в корпусе от старого блока питания ноутбука.
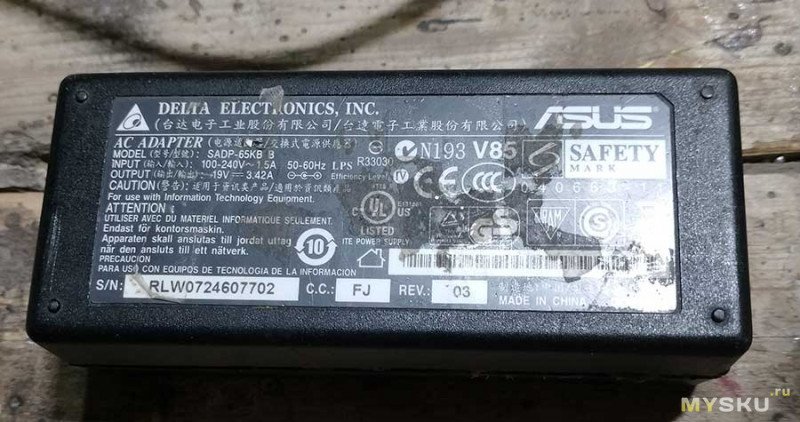
Кнопки были выпаяны, вместо них с торца корпуса установлен трех позиционный выключатель.
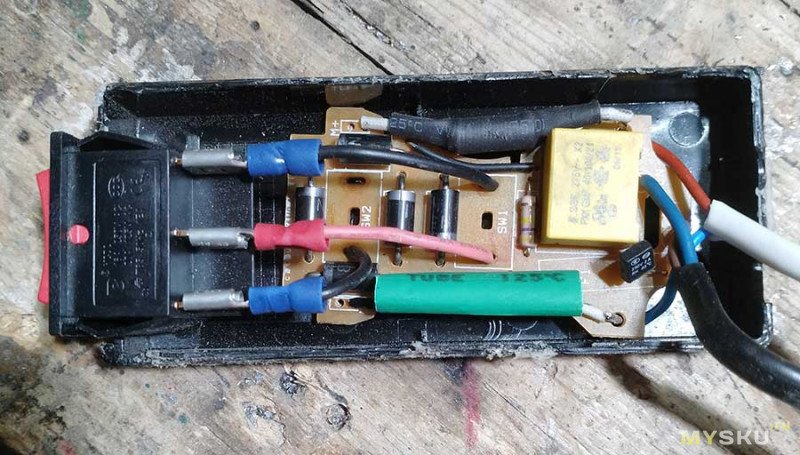
Результат многодневных усилий на фото ниже. Осталось только покрасить.
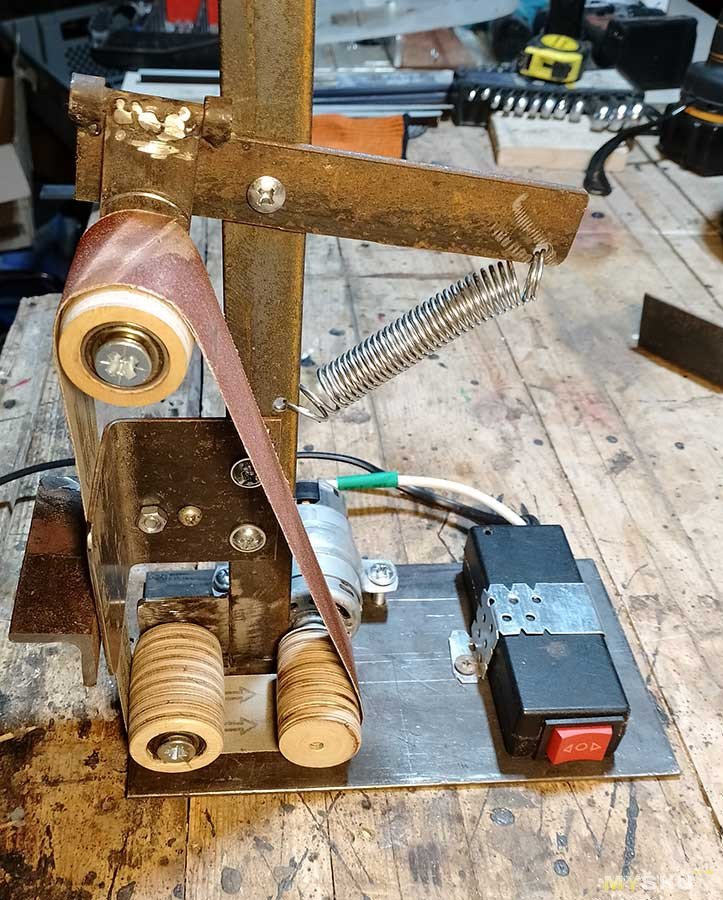
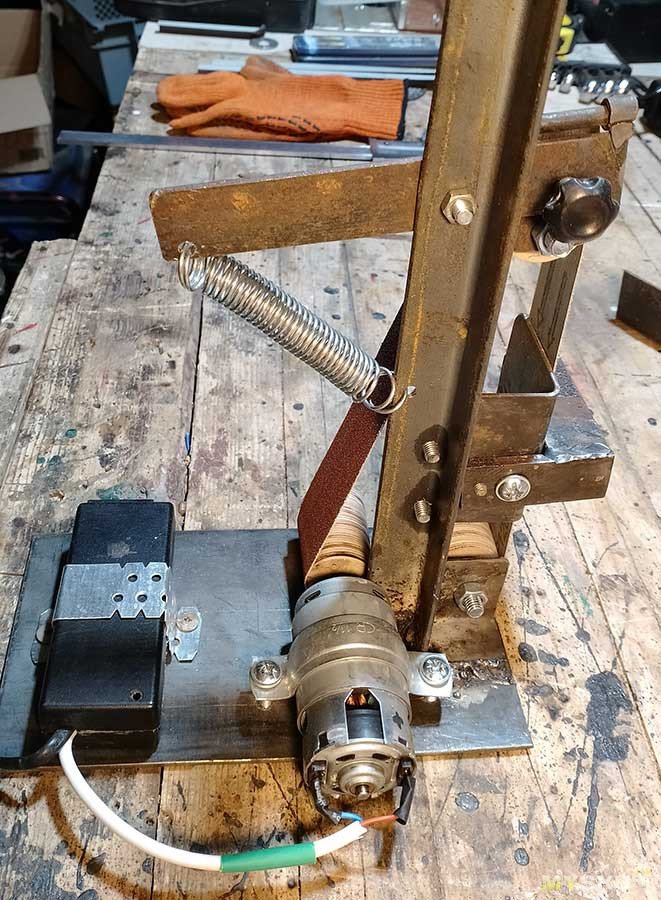
Каков же итог?
Гриндер работает. Довольно удобно затачивать сверла например. Но несмотря на большую мощность двигателя в 700Вт крутящий момент довольно слабый. При более менее сильном нажатии на ленту чувствуется как падает скорость движения. Особенно на малых оборотах. Так что, если нужно точить массивные детали лучше использовать двигатель от стиральной машины или аналогичный.
Как ни старался, но сварка деталей и отсутствие токарного станка дает небольшие погрешности при сборке. В итоге лента не всегда стабильна. Размещение двигателя с помощью хомута отдельно от стойки тоже не лучшая идея. Гораздо функциональнее закрепить все детали на одной вертикальной пластине, как это обычно сделано в промышленных гриндерах.
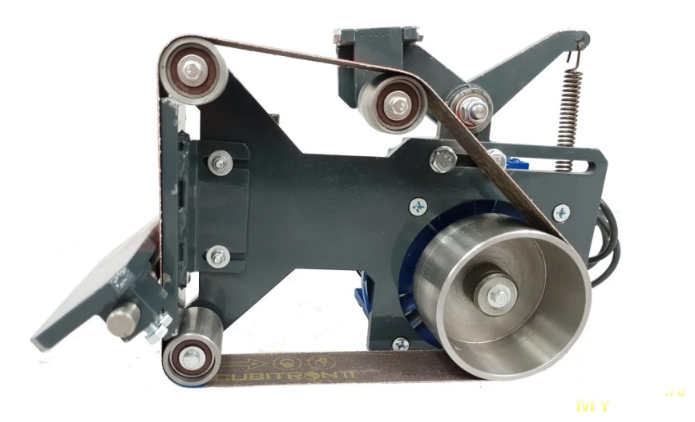
Еще нужно немного доработать мой вариант, а именно поставить улавливатель для опилок и защитную пластину возле блока питания и над верхним роликом. Хотя я не заметил, что оттуда летит стружка.
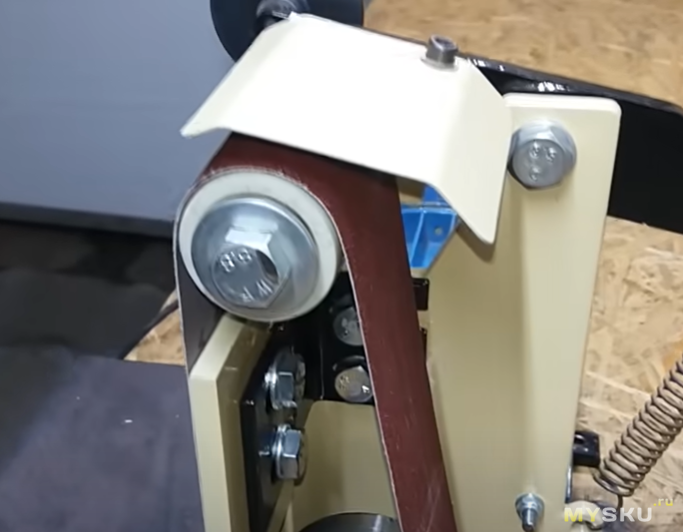
Самые обсуждаемые обзоры
+90 |
5021
136
|
+60 |
5539
95
|
Как вариант поставить ременную передачу от двигателя на ведущий вал.
Но в наличии не было нужных деталей
И даже наверное сможет карандаши затачивать)
А если серьёзно — я за свою жизнь видел ровной один самодельный — и при этом рабочий — токарник по металлу. И то большая часть деталей(направляйки, задняя бабка, столик) были взяты от заводского экземпляра, к которому была творчески
присприварена конструкция из шкивов, распорок и движка от швейной машинки, исполнявших роль шпинделя. Жёсткости в нём не было никакой, но люмишку оно грызло.ПС, в блендере нет поперечной нагрузки на вал двигателя, поставить бы вторую опору с подшипником на ведущий ролик.
ППС, сам не смог сделать нормальный гриндер, то мотора нет, то времени, то железа, в итоге на принтере напечатал маленький для макитовского аккумулятора с лентой шириной 30 мм и купил большой готовый. За руки всегда плюсую.
Здесь все файлы по проекту
Но главная проблема не в этом: у них крайне низкое время непрерывной работы, так же очень низкий ресурс и ОЧЕНЬ завышена мощность. То есть если написано 700 (а есть и 1200 в тех же габаритах) то это наверное только на КЗ при заблокированном валу. Он рассчитан на работу по несколько секунд пару раз в неделю. Если блендером начать месить что-то вязкое на несколько минут — срабатывает тепловая защита если повезёт, или тупо клинит двигатель, если не очень. Щёточный узел выходит из чата иногда со спецэффектами.
Что ещё за глупость мощность обмотки при коротком замыкании тока???
Хорошо хоть по гарантии заменили.
Последний такой супруга спалила на пасху (вот прошедшую) :)
потеря времени). И понимания, что стоило или купить ± готовый или прожить и без гриндера.работы в удовольствие на купленной, пусть не совершенной установке-станке-устройстве) наоборот расти.До сих пор пытаюсь доделать мини-столярный станок. В любом случае нужны знания как в механике, так и в электрике. Вдобавок есть масса нюансов — начиная от центровки валов и заканчивая выбором скорости и мощности двигателя. Любой незначительный просчет приводит к неудаче.
lifehack — забейте туда с ПВА стандартный шкант на 6мм. высохнет — пересверлите на нужный диаметр
Если нужно что-то более-менее нормальное, то цена будет уже совсем другая, неплохие гриндеры начинаются от 30к, хорошие — 50-60к, отличные — от 100к. Дело основное — в станине, жесткости и двигателе.
А втулка да, долго не проходит при таком количестве оборотов. Причем найти подобный движок с подшипниками еще надо постараться (либо поменять самостоятельно).
И не уверен что на таких оборотах и небольшом диаметре вала что-то получится.
Есть способ определения с помощью стробоскопа (в частности телефона). Там тоже на валу крепится полоска бумаги, но мне так и не удалось что-то определить этим методом.
>И не уверен что на таких оборотах и небольшом диаметре вала что-то получится.
Но ведь с магнитом и катушкой получилось?)
Стробоскоп с мобильником штука нестабильная, в мобильнике может быть автостабилизация частоты мерцания.
Даже просто моток проволоки.
Мне чтобы найти фотодиод, как минимум нужно поехать в город за 30км
В любом случае, я озвучил вариант измерения. Что делать с этой информацией потенциально заинтересованные разберутся самостоятельно.
А у меня валяется куча магнитов. Да и любой может достать из старого динамика.
Да, собственно, как можно в мастерской обходиться без магнита?
А вот с транзисторами засада…
Будет ли такая схема работать с оборотами в 35-40 тыс?
По оборотам — 40 тыщ в минуту это сильно меньше 1кгц, если мульт по размаху сигнала не будет возмущаться, то должно работать.
Скорее всего придется делать какой-то жесткий диск с пропилом для луча.
Кстати цимес еще и в том, что безбондажные варианты этих катков, самим производителям делаются «в бочку». Даже точить ничего не надо.
Ведь равновесие ленты получается неустойчивым.
Не проще ли сделать форму прямо противоположной,
дабы лента сама находила устойчивое положение?
И винт в этом случае станет не нужным… Нет?
кратко-примитивно, без векторов и формул: PS а из «ямы» (не путать с ребордами! для плоского ремня они в основном износ и потери увеличивают, но «держат») плоский ремень моментом вылетает… со свистом.
было дело, проверяли :)
На собственном опыте убедился, что это правда. Иногда видно, как лента уходит в сторону. но потом возвращается обратно
В общем-то чертежи нужны для расчета, а общий принцип и так понятен, если немного «инженерной фантазии» применить :)
Края ремня на бочке натянуты слабее, середина натянута сильно. Если скажем левый край решит съехать в сторону, правый окажется ближе к середине, натянется сильнее, и перетянет равновесие обратно на себя.
Именно. Попробуйте ее «выровнять в статике» — просто натягивая, без вращения.
PS Впрочем — оставим этот спор…
Я не собирась точить на гриндере топоры и стачивать полметра уголка 100.
Мне нужен для заточки сверл, ножей (не изготовлении, а именно для заточки), может подгонки какой-то детали из пластика или дерева.
Зачем мне на столе киловатный двигатель весом 25 кг и размером с пол стола?
Там — и, скорость регулируется стандартной кнопкой, и мощность под 0,6-0,8 kW.
И, размеры небольшие.
Кстати, при желании и реверсируется он…
Куда приехать забрать? :)))))
Прояснил, куда приезжать? ;)
Думаете ворочать барабан с 6кг белья на такой скорости проще?
В ролике ниже, вообще двигается (приводится двигателем) лишь точильный камень, обтачиваемый предмет вращается пассивно, в силу трения о него.
youtu.be/vHURCZ2otAo?si=eUJNtb8jxaTLoB9K&t=199